Control method of rolling mill capable of preventing slipping
A control method and anti-slip technology, which is applied in the field of cold rolling in the metallurgical field, can solve problems such as rack tension fluctuations and broken belts, and achieve the effects of ensuring rolling stability, improving accuracy, and avoiding slipping
- Summary
- Abstract
- Description
- Claims
- Application Information
AI Technical Summary
Problems solved by technology
Method used
Image
Examples
Embodiment 1
[0045] Production status: The production specification of the rolling mill is 3.5mm / 0.8mm×1413mm, when the tension setting value before the 3 stands is T SET(3) It is 38KN, and the setting value of rear tension is T SET(2) 42KN, rolling speed V 3 When it is 895mpm, the mill stand 3 slips, and the forward slip value f 3 It is -1.23%. Due to the slippage of the 3rd stand, the strip steel in the rolling mill stand shakes, and the thickness of the stand fluctuates greatly, which affects the stable production of the rolling mill.
[0046] Adjustment status: put into the rolling mill anti-skid control function and debug. First adjust the front tension adjustment amount T of the 3 racks slip(3) , the key here is to determine the increment ξ and the rate of change of ξ each time. The process of determining ξ is: (0.8KN→0.7KN→0.6KN→0.5KN), and the process of determining the step change rate of ξ is: (0.8KN / 20ms→0.4KN / 20ms→0.2KN / 20ms→0.1KN / 20ms). In order to improve the responsivenes...
Embodiment 2
[0047] Embodiment 2: (When the 3-frame slips, the slippage is eliminated by adjusting the front tension and the rear tension of the 3-frame)
[0048] Production status: The production specification of the rolling mill is 3.0mm / 0.5mm×1200mm, when the tension setting value before the 3 stands is T SET(3) It is 29KN, and the setting value of rear tension is T SET(2) 34KN, rolling speed V 3 When it is 901mpm, the rolling mill 3 stand slips, at this time the forward slip value f 3 It is -1.3%. Due to the slippage of the 3rd stand, the strip steel in the rolling mill stand shakes, and the thickness of the stand fluctuates greatly, so the rolling mill cannot produce stably.
[0049] Adjustment status: put into the rolling mill anti-skid control function and debug. First, adjust with 3 racks each setting increment ξ0.5KN and ξ rate of change 0.1KN / 20ms until the pre-tension setting value T SET(3) When it is greater than 31.9KN (greater than X times the set value), the forward slid...
PUM
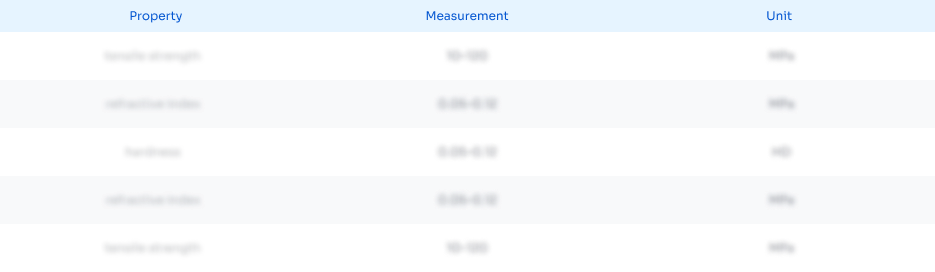
Abstract
Description
Claims
Application Information

- Generate Ideas
- Intellectual Property
- Life Sciences
- Materials
- Tech Scout
- Unparalleled Data Quality
- Higher Quality Content
- 60% Fewer Hallucinations
Browse by: Latest US Patents, China's latest patents, Technical Efficacy Thesaurus, Application Domain, Technology Topic, Popular Technical Reports.
© 2025 PatSnap. All rights reserved.Legal|Privacy policy|Modern Slavery Act Transparency Statement|Sitemap|About US| Contact US: help@patsnap.com