Assembling method of roller bearing
An assembly method and roller bearing technology, applied in the assembly field of roller bearings, can solve the problems of complex mold shape and opening and closing control, and increase manufacturing cost, so as to suppress the forming cost, suppress the mold cost, and reduce the possibility of cracks Effect
- Summary
- Abstract
- Description
- Claims
- Application Information
AI Technical Summary
Problems solved by technology
Method used
Image
Examples
Embodiment Construction
[0033] Embodiments of the present invention will be described below with reference to the drawings.
[0034] Such as figure 1 As shown, the case of applying to cylindrical roller bearings will be explained as an example. figure 1 Indicates the assembly process of cylindrical roller bearings. The assembly sequence is: Alternately arrange the rollers 16 and liners 18 on the inner periphery of the outer ring 14, and place the liners 18 that should be located on the two ribs of the last loaded roller 16 along the rolling surface 16a of the arranged rollers 16. After the inner diameter side of the bearing, the last roller 16 is pushed into the outer ring 14 so that the pads 18 of both ribs can be slid and the roller 16 can be incorporated.
[0035] The surface of the pad 18 that faces the roller rolling surface 16a, that is, the roller contact surface 18b has a concave shape that accommodates the roller rolling surface 16a. here, in figure 1 In the section perpendicular to t...
PUM
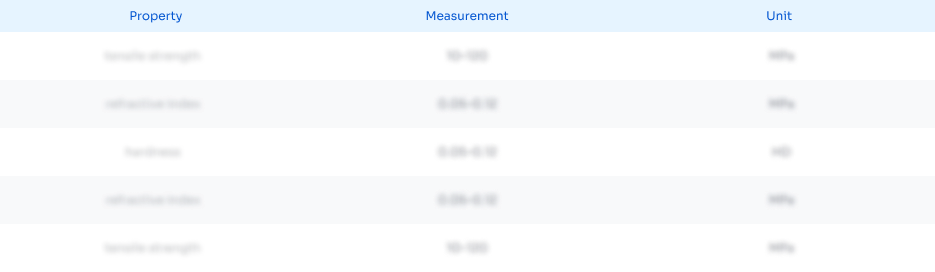
Abstract
Description
Claims
Application Information

- R&D
- Intellectual Property
- Life Sciences
- Materials
- Tech Scout
- Unparalleled Data Quality
- Higher Quality Content
- 60% Fewer Hallucinations
Browse by: Latest US Patents, China's latest patents, Technical Efficacy Thesaurus, Application Domain, Technology Topic, Popular Technical Reports.
© 2025 PatSnap. All rights reserved.Legal|Privacy policy|Modern Slavery Act Transparency Statement|Sitemap|About US| Contact US: help@patsnap.com