Non-linear procedure failure testing method based on two-dimensional dynamic kernel principal component analysis
A technology of dynamic core pivot and fault detection, applied in electrical testing/monitoring, instrumentation, character and pattern recognition, etc.
Inactive Publication Date: 2008-11-19
NORTHEASTERN UNIV
View PDF0 Cites 28 Cited by
- Summary
- Abstract
- Description
- Claims
- Application Information
AI Technical Summary
Problems solved by technology
Step 1: Determine sampling parameters
Method used
the structure of the environmentally friendly knitted fabric provided by the present invention; figure 2 Flow chart of the yarn wrapping machine for environmentally friendly knitted fabrics and storage devices; image 3 Is the parameter map of the yarn covering machine
View moreImage
Smart Image Click on the blue labels to locate them in the text.
Smart ImageViewing Examples
Examples
Experimental program
Comparison scheme
Effect test
example 1
example 2
the structure of the environmentally friendly knitted fabric provided by the present invention; figure 2 Flow chart of the yarn wrapping machine for environmentally friendly knitted fabrics and storage devices; image 3 Is the parameter map of the yarn covering machine
Login to View More PUM
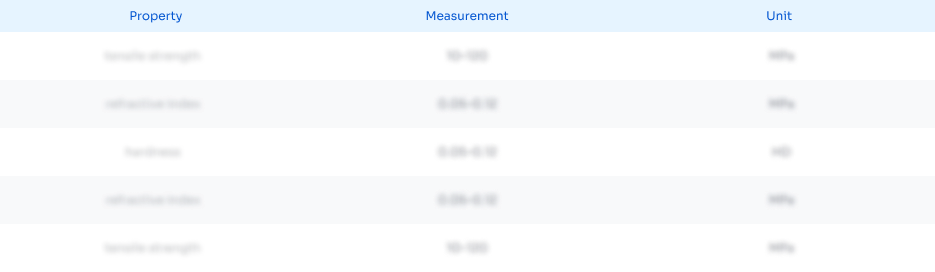
Abstract
Disclosed is a non-linear process fault detection method based on two-dimensional dynamic kernel principal component analysis, belonging to the fault detection technical field; the method comprises the following steps: the first step is to determine the sampling parameters, namely, to judge the execution process, determine the sampling parameters, select the data parameters which affect the fault, and then judge whether to carry through training or testing; the second step is training, that is, to collect the data of normal work, pick up the non-linear principal component of the training data through two-dimensional dynamic kernel principal component analysis, calculate the square prediction error of the training data and determine the control limit; the third step is testing, that is, to collect the online observation data, pick up the non-linear principal component of the online observation data through two-dimensional dynamic kernel principal component analysis, calculate the square prediction error of the real-time online observation data, compare the control limit of the square prediction error of the real-time online observation data with the control limit of the square prediction error of the training data, display and gives an alarm if the control limit of the former exceeds that of the latter. The invention can timely detect the fault in the production process and reduce losses in the industrial production process.
Description
Nonlinear Process Fault Detection Method Based on 2D Dynamic Kernel Principal Component Analysis technical field The invention belongs to the technical field of fault detection, in particular to a non-linear process fault detection method based on two-dimensional dynamic kernel principal component analysis (2D-DKPCA, TwoDimensionalDynamicKernelPrincipalComponentsAnalysis). Background technique With the continuous development of the economy, the number of industrial enterprises is increasing, and the competition among production departments is becoming increasingly fierce. To improve the efficiency of enterprises, it is necessary to improve product quality and reduce the number of substandard products. In addition to the higher and higher requirements for the production process of products, the requirements for the ability of fault detection methods in the production process are also higher and higher. This is because some failures are unavoidable in complex nonlinear prod...
Claims
the structure of the environmentally friendly knitted fabric provided by the present invention; figure 2 Flow chart of the yarn wrapping machine for environmentally friendly knitted fabrics and storage devices; image 3 Is the parameter map of the yarn covering machine
Login to View More Application Information
Patent Timeline

Patent Type & Authority Applications(China)
IPC IPC(8): G05B23/02G06K9/62
Inventor 张颖伟王婷周宏
Owner NORTHEASTERN UNIV
Features
- R&D
- Intellectual Property
- Life Sciences
- Materials
- Tech Scout
Why Patsnap Eureka
- Unparalleled Data Quality
- Higher Quality Content
- 60% Fewer Hallucinations
Social media
Patsnap Eureka Blog
Learn More Browse by: Latest US Patents, China's latest patents, Technical Efficacy Thesaurus, Application Domain, Technology Topic, Popular Technical Reports.
© 2025 PatSnap. All rights reserved.Legal|Privacy policy|Modern Slavery Act Transparency Statement|Sitemap|About US| Contact US: help@patsnap.com