Surface treating method of electric iron metal base plate
A metal base plate and surface treatment technology, which is applied in the direction of pretreatment surface, device for coating liquid on the surface, coating, etc., can solve the problems of uneven surface hardness and gloss, complicated production process, and low heat energy utilization rate , to achieve the effect of not easy to decolorize, low production cost and reduced complexity
- Summary
- Abstract
- Description
- Claims
- Application Information
AI Technical Summary
Problems solved by technology
Method used
Image
Examples
Embodiment Construction
[0038] The present invention will be further described below in conjunction with a preferred embodiment of the present invention.
[0039] The surface treatment method of the soleplate of the electric iron of the present invention includes the steps of base material treatment, paint curing, spraying process, drying and cooling, etc., wherein the base material treatment is divided into base material selection, base material pretreatment, sandblasting, cleaning, preheating and other five steps. stages, the detailed process is as follows:
[0040] A: Selection of base material: The base material needs to choose various aluminum alloys and stainless steel and other metal base materials as the bottom plate of the electric iron.
[0041] B: Substrate pretreatment: Substrate pretreatment includes the following steps:
[0042] 1. Substrate surface confirmation
[0043] (1) Whether the base material selection is appropriate: confirm the material, specification, quality, state, etc. o...
PUM
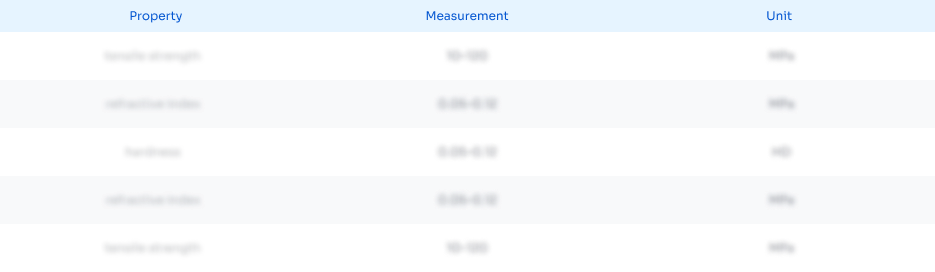
Abstract
Description
Claims
Application Information

- R&D Engineer
- R&D Manager
- IP Professional
- Industry Leading Data Capabilities
- Powerful AI technology
- Patent DNA Extraction
Browse by: Latest US Patents, China's latest patents, Technical Efficacy Thesaurus, Application Domain, Technology Topic, Popular Technical Reports.
© 2024 PatSnap. All rights reserved.Legal|Privacy policy|Modern Slavery Act Transparency Statement|Sitemap|About US| Contact US: help@patsnap.com