Continuous rolling and direct facing technique of middle (high) density beaverboard and equipment thereof
A density fiberboard and process equipment technology, which is applied in the jointing of wooden veneers, veneer presses, manufacturing tools, etc., can solve the problems of wasting materials and energy, endangering human health, complicating production lines, etc., and reduce energy consumption , no dust pollution, high production efficiency
- Summary
- Abstract
- Description
- Claims
- Application Information
AI Technical Summary
Problems solved by technology
Method used
Image
Examples
Embodiment Construction
[0013] As shown in the figure, the continuous rolling medium (high) density fiberboard process line 1 adopted in the present invention includes a silo 11, a steel belt 12, a fiberboard substrate pressing roller 13, a fiberboard substrate main pressing roller 14, and a board output system 15. The veneer material conveying process line 2 of the present invention includes a blanking roll 21, and a tension roller combination 22 installed along the veneer material 28, an upper pressure roller 23, a lower pressure roller 24, a rubber groove 25, and a rubber extrusion roller 26. , wherein the tension roller combination is composed of three single rollers arranged in a staggered manner; the cot extrusion roller is composed of two single rollers that are misplaced relative to the bonding material 28, and the rubber groove 25 is provided with a glue roller 251. The technical equipment for direct bonding of the fiberboard and the veneer of the present invention is mainly the upper and lo...
PUM
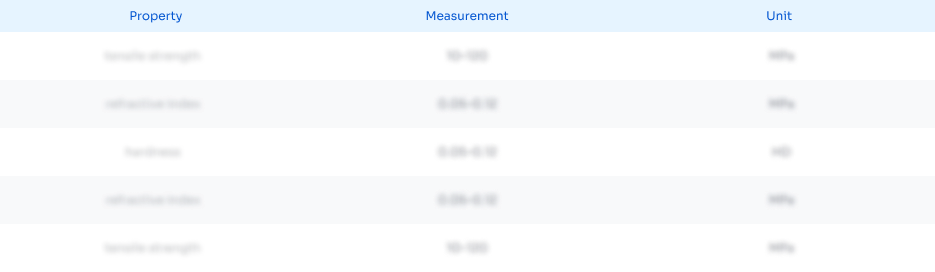
Abstract
Description
Claims
Application Information

- R&D
- Intellectual Property
- Life Sciences
- Materials
- Tech Scout
- Unparalleled Data Quality
- Higher Quality Content
- 60% Fewer Hallucinations
Browse by: Latest US Patents, China's latest patents, Technical Efficacy Thesaurus, Application Domain, Technology Topic, Popular Technical Reports.
© 2025 PatSnap. All rights reserved.Legal|Privacy policy|Modern Slavery Act Transparency Statement|Sitemap|About US| Contact US: help@patsnap.com