Air displacement stepless regulating method for reciprocating-piston compressor
A technology of compressor exhaust and stepless adjustment, applied in heating methods, mechanical equipment, machines/engines, etc., can solve problems such as the inability to effectively reduce the power consumption of compressors, and the inability to directly apply piston compressors, and achieves a reduction in the number of times, Increased reliability and reduced effect of pressure fluctuations
- Summary
- Abstract
- Description
- Claims
- Application Information
AI Technical Summary
Problems solved by technology
Method used
Image
Examples
Embodiment 1
[0034] With a speed of 980r / min and a rated displacement of 3m 3 / min single-stage air compressor as an example. Implementing the present invention requires an actuator and a control system that can press open the suction valve, and the control system operates as follows:
[0035] (1) Determine the characteristic parameter N of the actuator, which means that the actuator completes a complete set of actions, including pressing-holding-release, the minimum number of work cycles experienced, so N is determined by the response speed of the specific actuator. The characteristic parameter of the actuator in this embodiment is N=10, so a working unit is composed of 10 working cycles.
[0036] (2) The maximum displacement of the compressor at full load is Qm=3m 3 / min.
[0037] (3) Assume that the actual production required displacement Qr = 2.4m 3 / min, the duty cycle is:
[0038] R%=[Qr / Qm×100]%=[2.4 / 3×100]%=80%
[0039] (4) The actuator operates in the following way: with 100...
Embodiment 2
[0046] In Embodiment 1, 100 working units are taken as a control cycle, and the control cycle can be adjusted when a higher requirement is placed on the uniformity of the exhaust gas. The operation steps are as follows:
[0047] Steps (1), (2) are the same as in Example 1.
[0048] Step (3) still assumes that the actual production exhaust volume Qr=2.4m 3 / min, the duty cycle is:
[0049] R%=[Qr / Qm×100]%=[2.4 / 3×100]%=80%
[0050] (4) The actuator operates in the following manner: with 40 work cycles as a control cycle, 32 loading work units are executed first, and then 8 no-load work units are executed; the loading work unit accounts for 80% of the control cycle, and compression The machine still works according to the duty cycle.
[0051] (5) If the gas volume required for production has not changed, repeat the above step (4); if it needs to be changed, perform steps (3) to (4) to calculate with the new required gas volume.
[0052] For example, if the required gas volum...
Embodiment 3
[0057] Take a certain L-13 / 7-250 natural gas compressor as an example, the speed is 740r / min, and the rated displacement is 780m 3 / h, divided into 3 levels, a total of 3 cylinders, which are respectively cylinder 1, cylinder 2 and cylinder 3 according to the process. Implementing the present invention requires a centralized control system, and each of the three cylinders is equipped with an actuator that can press open the suction valve, and the centralized control system operates as follows:
[0058] (1) Determine the characteristic parameters N1, N2, and N3 of each actuator, which means that each actuator independently completes a complete set of actions, including the minimum number of work cycles experienced by pressing-holding-release, so N1~N3 is determined by the specific implementation The agency's speed of response will determine. The characteristic parameters of the actuator in this embodiment are N1=10, N2=20, N3=25.
[0059] (2) The maximum displacement of the c...
PUM
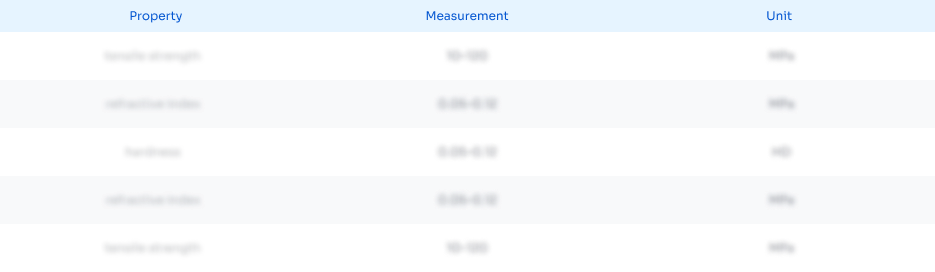
Abstract
Description
Claims
Application Information

- R&D
- Intellectual Property
- Life Sciences
- Materials
- Tech Scout
- Unparalleled Data Quality
- Higher Quality Content
- 60% Fewer Hallucinations
Browse by: Latest US Patents, China's latest patents, Technical Efficacy Thesaurus, Application Domain, Technology Topic, Popular Technical Reports.
© 2025 PatSnap. All rights reserved.Legal|Privacy policy|Modern Slavery Act Transparency Statement|Sitemap|About US| Contact US: help@patsnap.com