Control scheme for dc/ac cycloconverter
A converter and half-cycle technology, applied in the direction of converting irreversible DC power input to AC power output, conversion equipment that can be converted to DC without intermediate conversion, AC power input conversion to DC power output, etc.
- Summary
- Abstract
- Description
- Claims
- Application Information
AI Technical Summary
Problems solved by technology
Method used
Image
Examples
Embodiment Construction
[0053] specific implementation plan
[0054] With the known commutation scheme described above, the HF transformer 5 must be sized to receive the full DC link voltage in a 50% duty cycle. The magnetic material in the transformer must be sized to avoid saturation with the length of the applied power pulse. This scheme also has HF output inductor current commutation issues during low frequency zero current detection leading to premature burnout of commutation components and noise.
[0055] However, in the present invention, the controller 1 controls the HF inverter 3 and the cycloconverter 7 so that a more economical transformer 5 can be used. The controller 1 controls the switches S1, S2, S3 and S4 of the HF inverter 3 (FIG. 2) so that the switches S1 and S3 or the switches S2 and S4 are connected whenever the cycloconverter 7 is in the idle FW cycle. pass. This ensures that the voltage across the primary winding of the HF transformer 5 is short-circuited to zero when the cy...
PUM
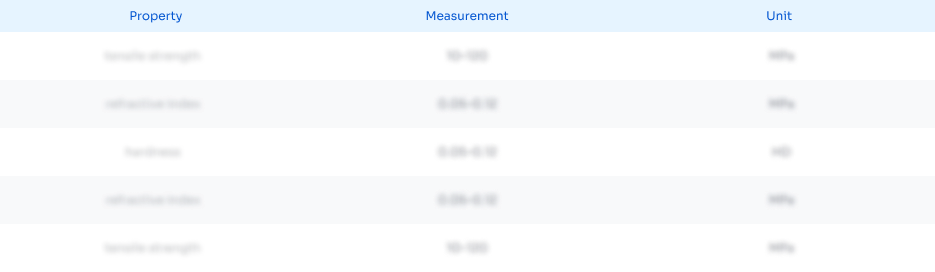
Abstract
Description
Claims
Application Information

- R&D Engineer
- R&D Manager
- IP Professional
- Industry Leading Data Capabilities
- Powerful AI technology
- Patent DNA Extraction
Browse by: Latest US Patents, China's latest patents, Technical Efficacy Thesaurus, Application Domain, Technology Topic, Popular Technical Reports.
© 2024 PatSnap. All rights reserved.Legal|Privacy policy|Modern Slavery Act Transparency Statement|Sitemap|About US| Contact US: help@patsnap.com