Device for printing plate-shaped work pieces
A workpiece and plate-shaped technology, which is applied in the field of devices for printing plate-shaped workpieces, can solve the problems such as the inability to maintain the working radius and the printing pattern tolerance.
- Summary
- Abstract
- Description
- Claims
- Application Information
AI Technical Summary
Problems solved by technology
Method used
Image
Examples
Embodiment Construction
[0032] An exemplary embodiment of the device according to the invention is schematically shown in plan view in FIG. 1 . Such a device is a printing press for simple direct printing or a first printing station for a multicolor printing press, the other printing stations of which are not shown for the sake of simplicity. The conveyor belt 1 runs through a printing nip 2 formed by a printing roller 3 designed as a gravure cylinder and a corresponding printing cylinder, not visible in plan view, arranged below the conveyor belt 1 . The height of the gravure printing cylinder 3 can be adjusted by means of a left adjusting motor 4 and a right adjusting motor 5 , wherein the two adjusting motors 4 and 5 can be operated independently of one another. Plate-shaped workpieces 7 are deposited on the front rollers 6 and are guided in the direction of travel indicated by arrow 8 towards the printing nip 2 where they are transferred to the conveyor belt 1 . Before that, the workpiece passes...
PUM
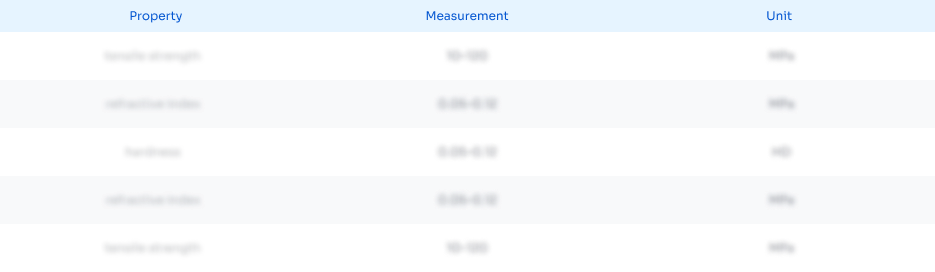
Abstract
Description
Claims
Application Information

- R&D Engineer
- R&D Manager
- IP Professional
- Industry Leading Data Capabilities
- Powerful AI technology
- Patent DNA Extraction
Browse by: Latest US Patents, China's latest patents, Technical Efficacy Thesaurus, Application Domain, Technology Topic, Popular Technical Reports.
© 2024 PatSnap. All rights reserved.Legal|Privacy policy|Modern Slavery Act Transparency Statement|Sitemap|About US| Contact US: help@patsnap.com