Contour outline control method for complicated track
A contour control and trajectory technology, applied in the direction of digital control, electrical program control, etc., can solve the problems of reducing contour performance, limiting the scope of application, and difficult to find implicit expressions.
- Summary
- Abstract
- Description
- Claims
- Application Information
AI Technical Summary
Problems solved by technology
Method used
Image
Examples
Embodiment Construction
[0064] A specific example embodiment is, see figure 1 Executing agencies, plane complex trajectory tracking and contour control examples.
[0065] figure 1 The diagram of the servo control mechanism, that is, shows the actual control platform for executing this example. 102 and 106 are XY-axis linear motion guide rails, connected together in a perpendicular manner, and fixed on the platform support of 101 mechanism; the travel position information of XY-axis is measured by the grating ruler, and the moving parts of 106 carry the actual work tasks; Front and rear limit switches 104 and return-to-origin switches are installed on each motion axis. The linear motion part is driven by the AC servo motor 105 through the servo amplifier to drive the ball screw, the speed information is returned by the motor encoder, and the position information is obtained by the 103 (X-axis) grating scale (equal distribution of the three axes). The servo motion structure of the vertical axis Z ...
PUM
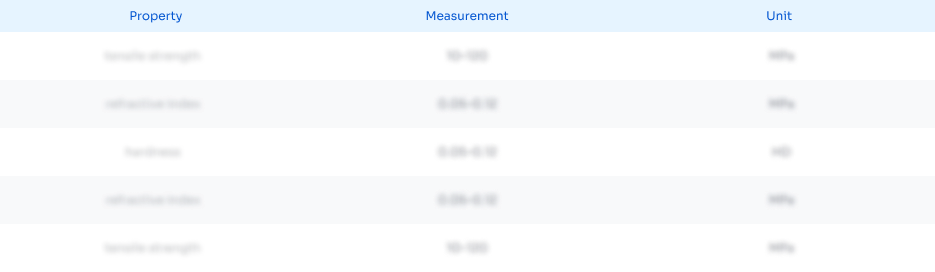
Abstract
Description
Claims
Application Information

- R&D
- Intellectual Property
- Life Sciences
- Materials
- Tech Scout
- Unparalleled Data Quality
- Higher Quality Content
- 60% Fewer Hallucinations
Browse by: Latest US Patents, China's latest patents, Technical Efficacy Thesaurus, Application Domain, Technology Topic, Popular Technical Reports.
© 2025 PatSnap. All rights reserved.Legal|Privacy policy|Modern Slavery Act Transparency Statement|Sitemap|About US| Contact US: help@patsnap.com