Two freedom space parallel mechanism
A technology with a degree of freedom and space, applied in the direction of manipulators, program-controlled manipulators, manufacturing tools, etc., can solve problems such as low flexibility, poor practicability, and large size, and achieve wide application prospects, high load capacity, and simple reverse solution. Effect
- Summary
- Abstract
- Description
- Claims
- Application Information
AI Technical Summary
Problems solved by technology
Method used
Image
Examples
Embodiment 1
[0032] Combine figure 1 , This embodiment includes fixed platform 1, Hooke hinge 2, movable platform 3, sliding rods 4 and 5, movable pairs 6 and 9, connecting rods 8 and 11, as well as spherical pairs 6, 10, 12, 13, and vertical rods 14. And 15, there are two moving pairs 6 and 9 on the moving platform 3, which are connected to the fixed platform 1 through three branches; two of the three branches have the same structure, and one branch of the two same structural branches includes one The sliding rod 4 and a connecting rod 8, the sliding rod 4 and the moving platform 3 are connected by a moving pair 6, one end of the connecting rod 8 and the sliding rod 4 are connected by a spherical pair 7, and the other end of the connecting rod 8 is connected with the fixed platform 1 by a spherical pair 13 connection; the other branch of the two same structural branches includes a sliding rod 5 and a connecting rod 11. The sliding rod 5 and the moving platform 3 are connected by a moving pai...
Embodiment 2
[0035] Combine figure 2 In this embodiment, the spherical pairs 12 and 13 connected between the connecting rods 8 and 11 and the fixed platform 1 in the embodiment 1 are replaced with Hooke hinges 17 and 16, and the other structures are the same as the embodiment 1.
Embodiment 3
[0037] Combine image 3 In this embodiment, the spherical pairs 7 and 10 connected between the connecting rods 8 and 11 and the sliding rods 4 and 5 in the first embodiment are replaced with Hooke hinges 18 and 19, and the other structures are the same as those in the first embodiment.
PUM
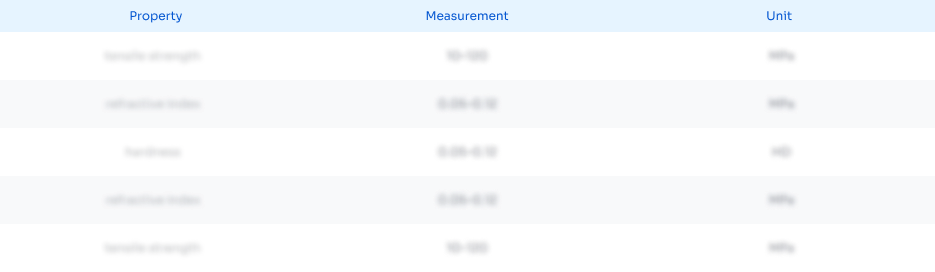
Abstract
Description
Claims
Application Information

- R&D
- Intellectual Property
- Life Sciences
- Materials
- Tech Scout
- Unparalleled Data Quality
- Higher Quality Content
- 60% Fewer Hallucinations
Browse by: Latest US Patents, China's latest patents, Technical Efficacy Thesaurus, Application Domain, Technology Topic, Popular Technical Reports.
© 2025 PatSnap. All rights reserved.Legal|Privacy policy|Modern Slavery Act Transparency Statement|Sitemap|About US| Contact US: help@patsnap.com