Un-drived self-adapted three-figure linage mechanism convenient for the handicapped having artificial hand
A linkage mechanism and under-actuated technology, applied in prosthetics, artificial arms, medical science, etc., can solve problems such as fingers and whole hands cannot maintain shape well, cannot maintain a grasping state, and cannot grasp objects stably, achieving The effect of light weight, increased stiffness, and high grip
- Summary
- Abstract
- Description
- Claims
- Application Information
AI Technical Summary
Problems solved by technology
Method used
Image
Examples
specific Embodiment approach 1
[0008] Specific implementation mode one: as figure 1 , figure 2 As shown, the underactuated self-adaptive three-finger linkage mechanism of the artificial hand for the disabled in this embodiment consists of a motor 1, a reducer 2, a motor seat 3, a three-finger base 6, a three-finger shaft 9, a middle finger transmission mechanism, and a ring finger transmission mechanism and the little finger transmission mechanism; the middle finger transmission mechanism is composed of small bevel gear 5, large bevel gear 8, gear retainer 10, middle finger torque sensor 7, middle finger drive torsion spring 12, middle finger spring support 22, middle finger first drive torsion spring Stop pin 11, middle finger second driving torsion spring stop pin 26 and middle finger sensor stop pin 27 are formed; described ring finger transmission mechanism is made up of ring finger torque sensor 21, ring finger driving torsion spring 19, ring finger spring support 18, ring finger first driving torsion...
specific Embodiment approach 2
[0010] Specific implementation mode two: as figure 1 As shown, the motor 1 of this embodiment is a stepping motor. Because the stepper motor has a reverse holding torque, it can maintain the gripping state when the power is lost. Other components and connections are the same as those in the first embodiment. The stepper motor in this embodiment is a two-phase permanent-magnet stepper motor manufactured by Portestcap Corporation with a model number of P110-06-2.5.
specific Embodiment approach 3
[0011] Specific implementation mode three: as figure 1 , figure 2 As shown, the middle finger torque sensor 7 , the ring finger torque sensor 21 , the little finger torque sensor 17 and the third finger shaft 9 in this embodiment are all clearance fit. With such a structure, the middle finger torque sensor 7 , the ring finger torque sensor 21 , and the little finger torque sensor 17 do not completely move synchronously with the three-finger shaft 9 to realize the adaptability of the three fingers to grasp different objects. Other components and connections are the same as those in the first embodiment.
PUM
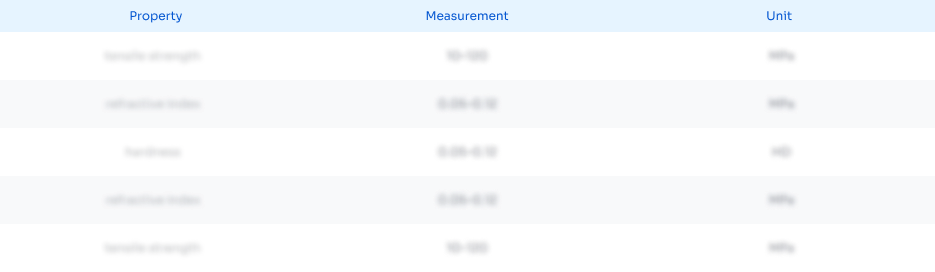
Abstract
Description
Claims
Application Information

- Generate Ideas
- Intellectual Property
- Life Sciences
- Materials
- Tech Scout
- Unparalleled Data Quality
- Higher Quality Content
- 60% Fewer Hallucinations
Browse by: Latest US Patents, China's latest patents, Technical Efficacy Thesaurus, Application Domain, Technology Topic, Popular Technical Reports.
© 2025 PatSnap. All rights reserved.Legal|Privacy policy|Modern Slavery Act Transparency Statement|Sitemap|About US| Contact US: help@patsnap.com