Computer controlled hydraulic resistance device for a prosthesis and other apparatus
a computer controlled and hydraulic resistance technology, applied in the field of computer controlled hydraulic resistance devices for prostheses and other apparatuses, can solve the problems of amputees walking with a slightly unnatural gait, mechanical braking mechanisms that are difficult to keep adjusted properly, and it is not feasible to duplicate muscle contraction, etc., to achieve high resistance, slow the prosthesis, and the effect of high resistan
- Summary
- Abstract
- Description
- Claims
- Application Information
AI Technical Summary
Benefits of technology
Problems solved by technology
Method used
Image
Examples
Embodiment Construction
[0055]In reference to FIG. 1, a typical lower limb prosthesis for an above-knee amputee includes a residual limb socket 1 which functions as an interface between the amputee and the prosthesis, a knee control assembly or unit 2 which provides knee rotation and resistance to aid in walking, a mounting pylon 3 and a foot 4. The components 1, 3 and 4 are conventional and commercially available.
[0056]The knee control assembly or unit 2 is described in connection with FIGS. 2-14 and includes a frame assembly 5 and an inverted U-shaped knee bracket 6 secured to the socket 1. The knee bracket 6 includes a right side retainer plate 7 and a left side retainer plate 8. The knee bracket 6 slides over opposite end portions of a rotor shaft 9 (FIG. 5), and each end portion has parallel flats to key the shaft to the bracket. The side retainer plates 7 and 8 are secured to the bracket 6 by screws, and the shaft 9 rotates with the knee bracket 6 relative to the frame 5. The left side retainer plate...
PUM
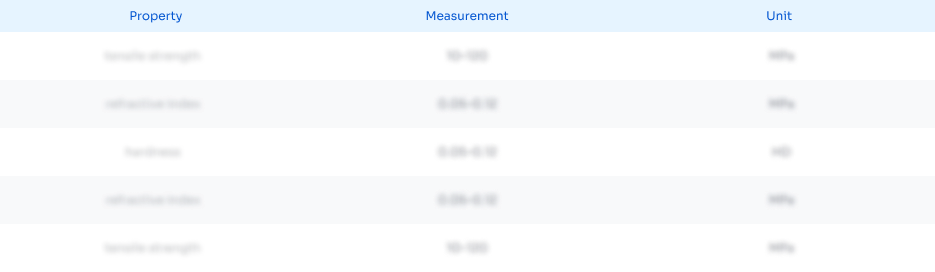
Abstract
Description
Claims
Application Information

- R&D
- Intellectual Property
- Life Sciences
- Materials
- Tech Scout
- Unparalleled Data Quality
- Higher Quality Content
- 60% Fewer Hallucinations
Browse by: Latest US Patents, China's latest patents, Technical Efficacy Thesaurus, Application Domain, Technology Topic, Popular Technical Reports.
© 2025 PatSnap. All rights reserved.Legal|Privacy policy|Modern Slavery Act Transparency Statement|Sitemap|About US| Contact US: help@patsnap.com