Excavation control system providing machine placement recommendation
a control system and excavating machine technology, applied in the direction of program control, navigation instruments, instruments, etc., can solve the problems of difficulty in positioning the excavating machine, material near the obstacle, damage to the machine and/or the obstacle,
- Summary
- Abstract
- Description
- Claims
- Application Information
AI Technical Summary
Benefits of technology
Problems solved by technology
Method used
Image
Examples
Embodiment Construction
[0012]FIG. 1 illustrates an exemplary machine 100 for use in industries such as mining, construction, farming, transportation, or any other industry known in the art. Machine 100 may be, for example, a backhoe, a dozer, a loader, an excavator, a motor grader, a dump truck, or any other excavating machine known in the art. Machine 100 may include an earthmoving implement 102, such as a bucket, a shovel, a blade, a fork-arrangement, a grasping device, and the like. Implement 102 may be operably connected to machine 100 by way of a linkage system 104 comprising one or more interconnected arm members 104a-d.
[0013]One or more actuators 106 may be operably interconnected between arm members 104a-d to position and / or orient implement 102 with respect to machine 100 in a preferred manner. Actuators 106 may include, for example, one or more of a hydraulic or pneumatic cylinder, a pump, a motor, or any other type of actuator known in the art. Machine 100 may further include an operator cabin...
PUM
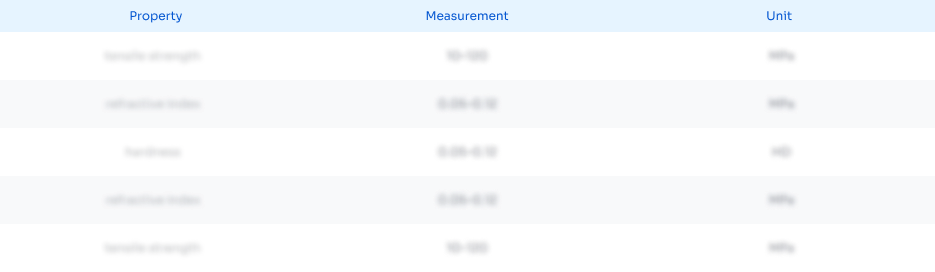
Abstract
Description
Claims
Application Information

- R&D
- Intellectual Property
- Life Sciences
- Materials
- Tech Scout
- Unparalleled Data Quality
- Higher Quality Content
- 60% Fewer Hallucinations
Browse by: Latest US Patents, China's latest patents, Technical Efficacy Thesaurus, Application Domain, Technology Topic, Popular Technical Reports.
© 2025 PatSnap. All rights reserved.Legal|Privacy policy|Modern Slavery Act Transparency Statement|Sitemap|About US| Contact US: help@patsnap.com