Actuator
A technology of actuators and bases, applied in instruments, piezoelectric devices/electrostrictive devices, piezoelectric/electrostrictive/magnetostrictive devices, etc., can solve the problem of increased cost, huge amount of data, and difficult displacement Correction control in the direction of recovery, etc., to achieve high reliability
- Summary
- Abstract
- Description
- Claims
- Application Information
AI Technical Summary
Problems solved by technology
Method used
Image
Examples
Embodiment Construction
[0053] Hereinafter, embodiments of an actuator and a device including the actuator according to the present invention will be described with reference to the drawings.
[0054] First, refer to figure 1 . figure 1 It is a schematic exploded perspective view showing the actuator 100 of this embodiment. The actuator 100 is manufactured using micromachining technology using semiconductor manufacturing processes and MEMS technology.
[0055] The actuator 100 includes: a base 1; a movable part 7 capable of displacing relative to the base 1; and 13c; and a plurality of drive portions 6a, 6b, and 6c for displacing the movable portion 7 relative to the base 1 .
[0056] The susceptor 1 includes a silicon member 1a, and a silicon nitride-based insulating layer 1b formed on the silicon member 1a. A driving circuit (not shown in the figure) is formed on the silicon member 1a. The drive units 6a to 6c are provided on the insulating layer 1b. Via holes (not shown in the figure) are ...
PUM
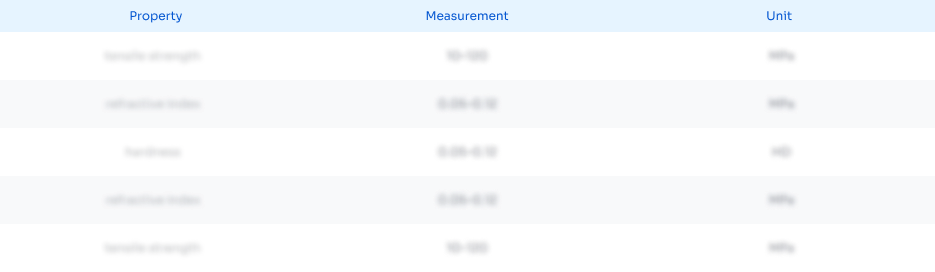
Abstract
Description
Claims
Application Information

- R&D
- Intellectual Property
- Life Sciences
- Materials
- Tech Scout
- Unparalleled Data Quality
- Higher Quality Content
- 60% Fewer Hallucinations
Browse by: Latest US Patents, China's latest patents, Technical Efficacy Thesaurus, Application Domain, Technology Topic, Popular Technical Reports.
© 2025 PatSnap. All rights reserved.Legal|Privacy policy|Modern Slavery Act Transparency Statement|Sitemap|About US| Contact US: help@patsnap.com