Track adaptive torque gearing mechanism
A torque transmission mechanism, self-adaptive technology, applied in mechanical equipment, transmission, belt/chain/gear, etc.
- Summary
- Abstract
- Description
- Claims
- Application Information
AI Technical Summary
Problems solved by technology
Method used
Image
Examples
Embodiment approach 1
[0016] It consists of mechanical arms 1 and 2 with two rotational degrees of freedom, chain transmission devices 3 and 4, sprockets 5, 6, 7 and 8, end tooth coupling 9, universal joint 10 and counterweight device 11; the chain transmission device 3 and 4 and the sprockets 5, 6, 7 and 8 are respectively placed in the shells of the mechanical arms 1 and 2, and the sprockets 5, 6, 7 and 8 are fixed as one with the rotating shafts of the mechanical arms 1 and 2, and the universal joints 10 is connected to the shaft of the mechanical arm 2 through the end gear coupling 9; The angle of the two rotational degrees of freedom of robotic arms 1 and 2 is 0 degrees, and the direction of rotation is clockwise. The end-tooth coupling 9 is provided with 8 pairs of tooth slots connecting the shaft of the mechanical arm and the shaft of the universal joint. After engaging with the tooth slots through 8 pairs of teeth, the nuts are fastened to form a whole.
Embodiment approach 2
[0018] It consists of mechanical arms 1 and 2 with two rotational degrees of freedom, chain transmission devices 3 and 4, sprockets 5, 6, 7 and 8, end tooth coupling 9, universal joint 10 and counterweight device 11; the chain transmission device 3 and 4 and the sprockets 5, 6, 7 and 8 are respectively placed in the shells of the mechanical arms 1 and 2, and the sprockets 5, 6, 7 and 8 are fixed as one with the rotating shafts of the mechanical arms 1 and 2, and the universal joints 10 is connected to the shaft of the mechanical arm 2 through the end gear coupling 9; The angle of the two rotational degrees of freedom of mechanical arms 1 and 2 is 90 degrees, and the direction of rotation is counterclockwise. The end-tooth coupling 9 is provided with 8 pairs of tooth slots connecting the shaft of the mechanical arm and the shaft of the universal joint. After engaging with the tooth slots through 8 pairs of teeth, the nuts are fastened to form a whole.
Embodiment approach 3
[0020] It consists of mechanical arms 1 and 2 with two rotational degrees of freedom, belt transmission devices 3 and 4, pulleys 5, 6, 7 and 8, end tooth coupling 9, universal joint 10 and counterweight device 11; the belt transmission device 3 and 4 and the pulleys 5, 6, 7 and 8 are respectively placed in the shells of the mechanical arms 1 and 2, and the pulleys 5, 6, 7 and 8 are fixed as one with the rotating shafts of the mechanical arms 1 and 2, and the universal joints 10 is connected to the shaft of the mechanical arm 2 through the end gear coupling 9; The angle of the two rotational degrees of freedom of the mechanical arms 1 and 2 is 360 degrees, and the direction of rotation is clockwise. The end-tooth coupling 9 is provided with 8 pairs of tooth slots connecting the shaft of the mechanical arm and the shaft of the universal joint. After engaging with the tooth slots through 8 pairs of teeth, the nuts are fastened to form a whole.
PUM
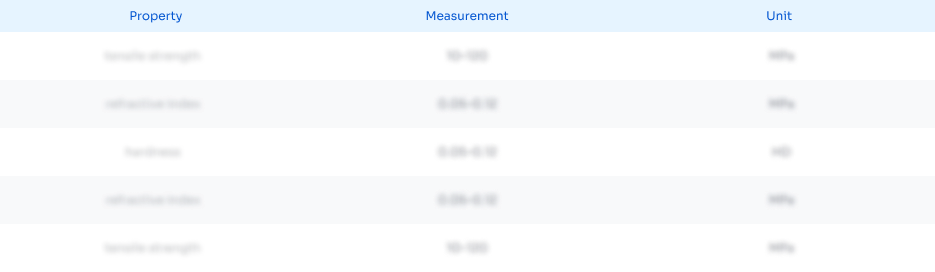
Abstract
Description
Claims
Application Information

- R&D
- Intellectual Property
- Life Sciences
- Materials
- Tech Scout
- Unparalleled Data Quality
- Higher Quality Content
- 60% Fewer Hallucinations
Browse by: Latest US Patents, China's latest patents, Technical Efficacy Thesaurus, Application Domain, Technology Topic, Popular Technical Reports.
© 2025 PatSnap. All rights reserved.Legal|Privacy policy|Modern Slavery Act Transparency Statement|Sitemap|About US| Contact US: help@patsnap.com