Anti-scooping connector plug, anti-scooping connector socket and connector assembly
A connector plug and plug technology, which is applied to the parts, connections, and contact parts of the connection device, can solve the problems of unsatisfactory requirements, small overall size, and inability to realize the anti-scooping function, so as to facilitate product floating installation, The effect of simple product installation
- Summary
- Abstract
- Description
- Claims
- Application Information
AI Technical Summary
Problems solved by technology
Method used
Image
Examples
Embodiment Construction
[0030] The technical solutions of the present invention will be further described in detail below with reference to the accompanying drawings and preferred embodiments.
[0031] An embodiment of a scoop-proof connector assembly, such as Figure 3 to Figure 9 As shown in the figure, it includes the anti-scoop connector plug 1 and the anti-scoop connector socket 2 that are adapted and plugged, so that the opposite ends of the anti-scoop connector plug and the anti-scoop connector socket are used as respective front ends, and the anti-scoop connector socket is used as the front end. The connector socket includes a socket insulator 3, a socket 4 and a pressure plate 5. The socket 4 is installed in the pressure plate 5, and the pressure plate 5 is installed in the socket insulator 3. The socket 4 is provided with two rows, and each row of sockets is along the width direction of the socket. Set six. The anti-scooping connector plug includes a plug insulator 6 and a pin 7 assembled ...
PUM
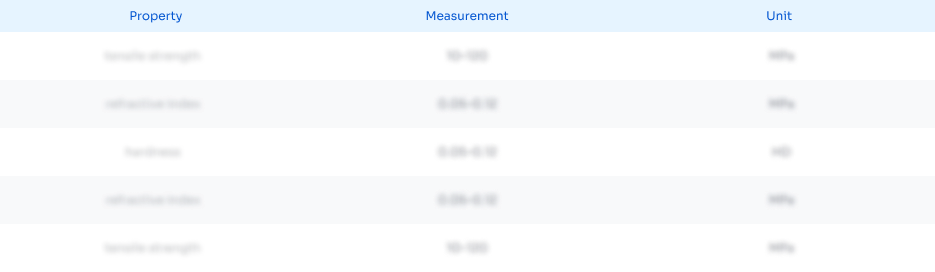
Abstract
Description
Claims
Application Information

- R&D
- Intellectual Property
- Life Sciences
- Materials
- Tech Scout
- Unparalleled Data Quality
- Higher Quality Content
- 60% Fewer Hallucinations
Browse by: Latest US Patents, China's latest patents, Technical Efficacy Thesaurus, Application Domain, Technology Topic, Popular Technical Reports.
© 2025 PatSnap. All rights reserved.Legal|Privacy policy|Modern Slavery Act Transparency Statement|Sitemap|About US| Contact US: help@patsnap.com