Soft operating arm based on cross-modal tactile sensor and bubble driver
A tactile sensor and driver technology, applied in the direction of program control manipulators, manufacturing tools, chucks, etc., can solve the problem of lack of durable, reliable, versatile software tactile sensors, tactile sensing technology application and commercialization lag, increasing system complexity To achieve the effect of safe human-computer interaction, safe unlimited freedom, and simple production method
- Summary
- Abstract
- Description
- Claims
- Application Information
AI Technical Summary
Problems solved by technology
Method used
Image
Examples
Embodiment 1
[0038] Refer to the manual attached figure 1 to the attached Figure 10 , based on the software operating arm of the cross-modal tactile sensor and the bubble driver, the bubble driver 3 is arranged between the triangular acrylic support plate 2, and the three bubble drivers 3 are equally spaced around the center at the three vertices of the triangular acrylic support plate 2 Position, the bubble driver 3 is provided with the spring 4 between each other, and the two ends of the spring 4 are fixedly connected with the side of the triangular acrylic support plate 2 that is close to each other, and the three springs 4 are distributed in the position of the center of the edge line of the triangular acrylic support plate 2. To support, the side wall of the top triangular acrylic support plate 2 is fixedly connected with the surface of the square acrylic fixing plate 1, and the bottom surface of the bottom triangular acrylic support plate 2 is fixed with three software pneumatic fin...
Embodiment 2
[0040] Based on the first embodiment, refer to the appendix of the specification figure 1 to the attached Figure 10 , Based on the software operating arm of the cross-modal tactile sensor and the bubble driver, the bubble driver 3 uses PE plastic film as the main material, and uses the triangular acrylic support plate 2 after the through hole to divide the PE plastic film into many retractable small bubbles, three The spring 4 is distributed at the center of the edge of the triangular acrylic support plate 2, and plays a supporting role. The axial expansion and contraction can be achieved by inflating and deflating a single bubble driver 3, while the drive system composed of multiple bubble drivers 3 can be provided by providing Different air intake rates make it bend at a certain angle, so as to realize the bending motion of the robot arm with infinite degrees of freedom;
[0041] The soft film 6 uses the camera module 7 to collect the deformed image of the columnar protrus...
PUM
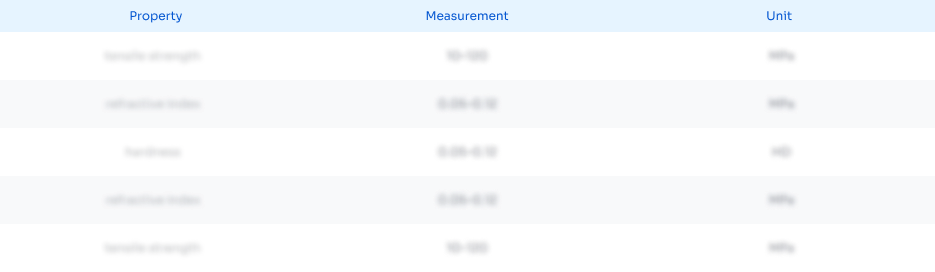
Abstract
Description
Claims
Application Information

- Generate Ideas
- Intellectual Property
- Life Sciences
- Materials
- Tech Scout
- Unparalleled Data Quality
- Higher Quality Content
- 60% Fewer Hallucinations
Browse by: Latest US Patents, China's latest patents, Technical Efficacy Thesaurus, Application Domain, Technology Topic, Popular Technical Reports.
© 2025 PatSnap. All rights reserved.Legal|Privacy policy|Modern Slavery Act Transparency Statement|Sitemap|About US| Contact US: help@patsnap.com