Rotary drilling rig power head structure with buffer mechanism
A buffer mechanism and buffer structure technology, applied in the direction of impact drilling, rotary drilling, drilling equipment, etc., can solve problems such as increasing the risk of motor damage, and achieve the effect of increasing the applicable range and enhancing protection.
- Summary
- Abstract
- Description
- Claims
- Application Information
AI Technical Summary
Problems solved by technology
Method used
Image
Examples
Embodiment
[0026] Example: such as Figure 1 to Figure 7 As shown, the present invention provides a rotary drilling power head structure with a buffer mechanism, including a power box 1, a radial buffer structure 6 arranged inside the power box 1, a driving force main shaft 9 is arranged at the center of the power box 1, The driving force main shaft 9 is sleeved with a gear set that is mutually locked with the radial buffer structure 6; the radial buffer structure 6 includes an upper chute 601 arranged on the inner ring of the power box 1, which The lower chute 602 below 601, the first gear clip 13 sliding inside the upper chute 601, and the second gear clip 14 sliding in the inner cavity of the lower chute 602, the upper chute 601 and the lower chute Both ends of 602 are equipped with magnets 603. The first gear bar 13 is provided with a pair of first opposite magnets 15 to slide inside the upper chute 601. The second gear bar 14 is provided with a pair of second magnets. The opposite ...
PUM
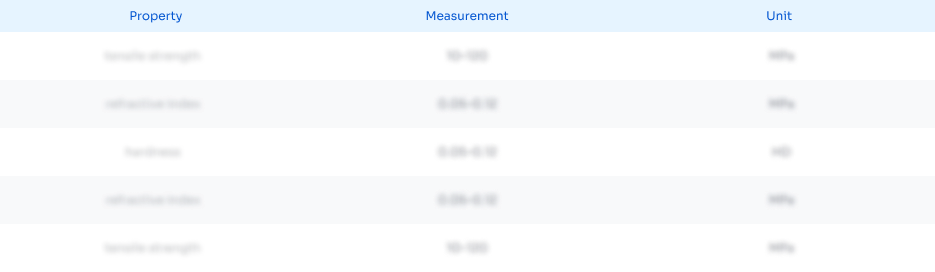
Abstract
Description
Claims
Application Information

- Generate Ideas
- Intellectual Property
- Life Sciences
- Materials
- Tech Scout
- Unparalleled Data Quality
- Higher Quality Content
- 60% Fewer Hallucinations
Browse by: Latest US Patents, China's latest patents, Technical Efficacy Thesaurus, Application Domain, Technology Topic, Popular Technical Reports.
© 2025 PatSnap. All rights reserved.Legal|Privacy policy|Modern Slavery Act Transparency Statement|Sitemap|About US| Contact US: help@patsnap.com