Wind power generation speed-increasing gearbox planet carrier cylindrical roller bearing with stop groove
A technology of cylindrical roller bearings and cylindrical rollers, applied in the field of bearings, can solve problems affecting the use of bearings, damage to cylindrical rollers, and low service life, and achieve the effects of avoiding bearing wear, good sealing effect, and easy installation
- Summary
- Abstract
- Description
- Claims
- Application Information
AI Technical Summary
Problems solved by technology
Method used
Image
Examples
Embodiment
[0032] Example: Please refer to Figure 1 to Figure 8 :
[0033] The present invention proposes a cylindrical roller bearing for a planetary frame of a wind power generation gearbox with a stop groove, comprising: an inner ring body 1, an outer ring body 2, an inner spacer ring 3 and a sealing ring body 4;
[0034] The inner ring body 1 is clamped on the inner side of the outer ring body 2, and the inner ends of the inner ring body 1 and the outer ring body 2 are respectively rotated and fitted with a sealing ring body 4. The inner ring body 1 includes an inner ring ring 101 and cylindrical rollers. A102, the outer ring of the inner ring 101 is provided with an outer concave ring groove 1011, and ten sets of cylindrical rollers A102 are rotated in the outer concave ring groove 1011, and the outer ring body 2 includes a semicircular plate 201 and cylindrical rollers B202, There are two groups of semicircular plates 201, and inner grooves 2011 are respectively arranged on the i...
PUM
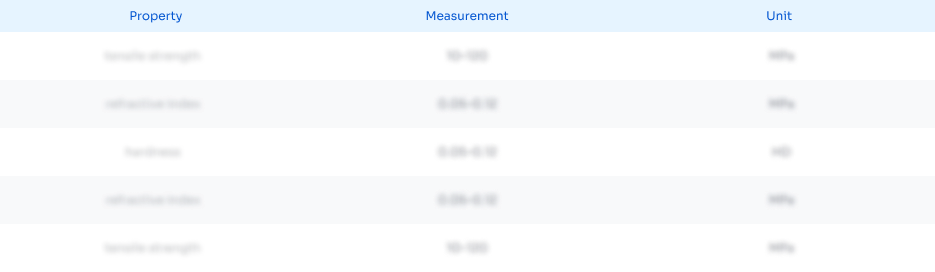
Abstract
Description
Claims
Application Information

- R&D Engineer
- R&D Manager
- IP Professional
- Industry Leading Data Capabilities
- Powerful AI technology
- Patent DNA Extraction
Browse by: Latest US Patents, China's latest patents, Technical Efficacy Thesaurus, Application Domain, Technology Topic, Popular Technical Reports.
© 2024 PatSnap. All rights reserved.Legal|Privacy policy|Modern Slavery Act Transparency Statement|Sitemap|About US| Contact US: help@patsnap.com