Point-to-point iterative learning minimum energy control method for double-rotor pneumatic system
A minimum energy control, pneumatic system technology, applied in the direction of adaptive control, general control system, control/regulation system, etc., can solve the problem of system failure to respond, and achieve the effect of reducing energy loss
- Summary
- Abstract
- Description
- Claims
- Application Information
AI Technical Summary
Problems solved by technology
Method used
Image
Examples
Embodiment Construction
[0161] The specific embodiments of the present invention will be further described below in conjunction with the accompanying drawings.
[0162] Such as figure 1 As shown, the input signal of the kth batch of DC motors is u k , apply it to the dual-rotor pneumatic system to get the output signal y of the kth batch system k . For the point-to-point tracking problem, the jth batch of Λ will be stored in the tracking time point distribution memory j Acting on the conversion module, the output signal y will be output through the conversion module k converted to its point-to-point output signal After that, the point-to-point output signal will be and the set expected value r stored in the point-to-point expected trajectory memory p Compare to get the point-to-point tracking error If the error accuracy does not reach the set accuracy, the point-to-point tracking error with current controller input u k passed to the norm-optimized iterative learning controller to generat...
PUM
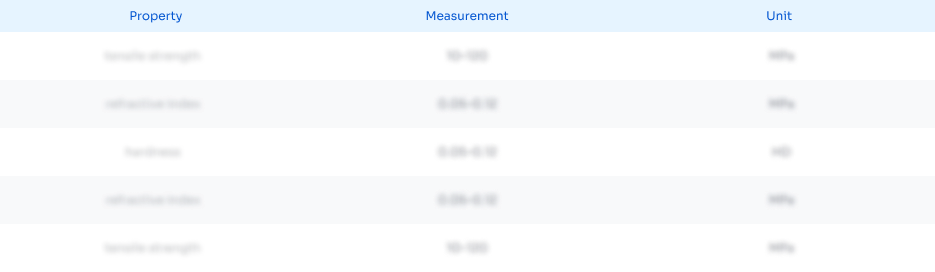
Abstract
Description
Claims
Application Information

- R&D Engineer
- R&D Manager
- IP Professional
- Industry Leading Data Capabilities
- Powerful AI technology
- Patent DNA Extraction
Browse by: Latest US Patents, China's latest patents, Technical Efficacy Thesaurus, Application Domain, Technology Topic, Popular Technical Reports.
© 2024 PatSnap. All rights reserved.Legal|Privacy policy|Modern Slavery Act Transparency Statement|Sitemap|About US| Contact US: help@patsnap.com