Omni-directional mobile robot docking mechanism control system and method based on visual guidance
A docking mechanism, omnidirectional movement technology, applied in the direction of program-controlled manipulators, manipulators, manufacturing tools, etc., can solve the problems of insufficient ability to obtain position and attitude deviation information, difficulty in the control system to complete tasks, and limited docking range. The effect of adapting to the movement of the external environment, enhancing the pose accuracy, and avoiding maintenance difficulties
- Summary
- Abstract
- Description
- Claims
- Application Information
AI Technical Summary
Problems solved by technology
Method used
Image
Examples
Embodiment Construction
[0066] The reconfigurable omnidirectional mobile robot docking mechanism applied in the present invention is as follows: figure 1 As shown, it includes an active mobile module 1 and a passive mobile module 3 . The active mobile module 1 is connected with a mechanical arm 2, and the mechanical arm 2 is driven in series by a connecting rod. The end of the mechanical arm is connected with a floating joint 4, such as figure 2 As shown, the mechanical arm 2 is turned over by the mechanical arm motor 8, and can complete a vertical rotation angle of 230°. It means that the floating joint 4 is installed at the end of the mechanical arm 2, and can complete a passive circular swing of 10°. The passive mobile module 3 is provided with an active connector 11, and a locking mechanism 5 is provided between the passive connector and the active connector 11. The active connector 11 has a U-shaped docking groove. The locking mechanism 5 adopts a mobile open type The locking mechanism has a ...
PUM
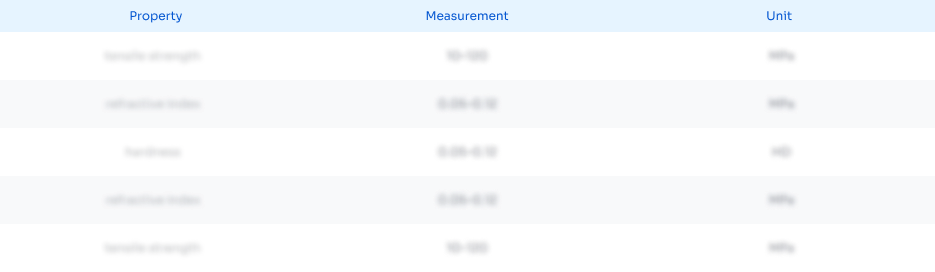
Abstract
Description
Claims
Application Information

- R&D
- Intellectual Property
- Life Sciences
- Materials
- Tech Scout
- Unparalleled Data Quality
- Higher Quality Content
- 60% Fewer Hallucinations
Browse by: Latest US Patents, China's latest patents, Technical Efficacy Thesaurus, Application Domain, Technology Topic, Popular Technical Reports.
© 2025 PatSnap. All rights reserved.Legal|Privacy policy|Modern Slavery Act Transparency Statement|Sitemap|About US| Contact US: help@patsnap.com