Variable stiffness transmission joint based on cam mechanism and switching control method
A technology of transmission joints and cam mechanisms, which is applied in the direction of program-controlled manipulators, manipulators, manufacturing tools, etc., can solve the problems of difficult control and poor stiffness retention of variable stiffness joints, and achieve high stiffness retention, compact structure, and simple control. Effect
- Summary
- Abstract
- Description
- Claims
- Application Information
AI Technical Summary
Problems solved by technology
Method used
Image
Examples
Embodiment Construction
[0050] In order to make the technical means, creative features, goals and effects achieved by the present invention easy to understand, the present invention will be further elaborated below in conjunction with the accompanying drawings and embodiments.
[0051] Such as Figure 1 to Figure 9 As shown, a variable stiffness transmission joint based on a cam mechanism includes a transmission module, a variable stiffness module, a large electromagnet 9 , a large spring 10 , a variable stiffness motor 19 and a reducer 21 located in the transmission module.
[0052] Specifically, such as figure 2 with image 3 As shown, the transmission module includes a rear axle I1, a front axle I5, an end cover 6, an axle II8, and a torsion bar 16.
[0053] Further, the rear axle I1 and the front axle I5 are fixedly connected by four sets of bolts 2 , washers 3 and nuts 4 uniformly distributed in the circumferential direction.
[0054] Both the rear axle I1 and the front axle I5 have cavities...
PUM
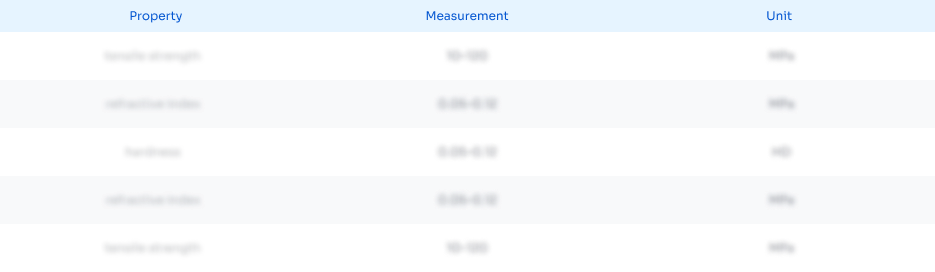
Abstract
Description
Claims
Application Information

- R&D Engineer
- R&D Manager
- IP Professional
- Industry Leading Data Capabilities
- Powerful AI technology
- Patent DNA Extraction
Browse by: Latest US Patents, China's latest patents, Technical Efficacy Thesaurus, Application Domain, Technology Topic, Popular Technical Reports.
© 2024 PatSnap. All rights reserved.Legal|Privacy policy|Modern Slavery Act Transparency Statement|Sitemap|About US| Contact US: help@patsnap.com