A laser profile sensor eye-in-hand calibration method based on a ladder-shaped calibration object
A calibration object and step-shaped technology, applied in the field of robot three-dimensional vision, can solve the problems of low precision and cumbersome calibration process, and achieve the effect of easy operation and strong industrial application potential.
- Summary
- Abstract
- Description
- Claims
- Application Information
AI Technical Summary
Problems solved by technology
Method used
Image
Examples
Embodiment Construction
[0062] Next, the present invention will be described in detail with reference to the drawings and specific embodiments. This embodiment is based on the premise of the technical solution of the present invention, giving detailed implementation and specific calibration process, but the embodiment of the present invention is not limited to the present invention.
[0063] The present invention proposes a laser profile sensor calibration method based on a stepped calibration object, which is characterized in that it comprises the following steps:
[0064] S1. Calibrate the tool coordinate system of the robot. The ladder-shaped calibration object is placed on the workbench processed by the robot, and the robot is used to calibrate the user coordinate system with the ladder-shaped calibration object;
[0065] S2. Control the robot to align the line laser of the laser profile sensor with each marking point on the stepped calibration object, scan the stepped calibration object at this ...
PUM
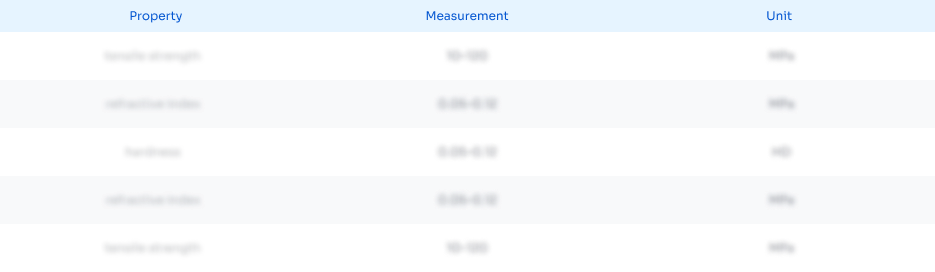
Abstract
Description
Claims
Application Information

- R&D
- Intellectual Property
- Life Sciences
- Materials
- Tech Scout
- Unparalleled Data Quality
- Higher Quality Content
- 60% Fewer Hallucinations
Browse by: Latest US Patents, China's latest patents, Technical Efficacy Thesaurus, Application Domain, Technology Topic, Popular Technical Reports.
© 2025 PatSnap. All rights reserved.Legal|Privacy policy|Modern Slavery Act Transparency Statement|Sitemap|About US| Contact US: help@patsnap.com