High-precision projection welding error compensation system based on robot hand-eye visual feedback
A technology of visual feedback and robot hand, applied in manipulators, program control manipulators, welding equipment, etc., can solve problems such as robot teaching welding trajectory deviation, achieve the effect of solving welding trajectory errors and improving welding accuracy and quality
- Summary
- Abstract
- Description
- Claims
- Application Information
AI Technical Summary
Problems solved by technology
Method used
Image
Examples
Embodiment Construction
[0026] Below in conjunction with the present invention in the accompanying drawings, the technical solution embodiment will be apparent to the present invention, completely described, obviously, the described embodiments are merely part of embodiments of the present invention rather than all embodiments.
[0027] Refer Figure 1-4 , Based on the visual feedback of the robot hand-eye projection welding precision error compensation system comprising a depth camera, welding apparatus 2, projection welding electrodes 3, 4 welding robot, welding holes target 5, a depth camera and projection welding the welding electrodes 3 are located in side apparatus 2, the target 5 placed under the welding hole 3 of projection welding, the welding robot 4 is located outside the welding apparatus 2.
[0028] The system works as follows:
[0029] 1, first robotic automation nut projection welding system for offline calibration parameters to be calibrated internal reference matrix K hand-eye camera, 6D ...
PUM
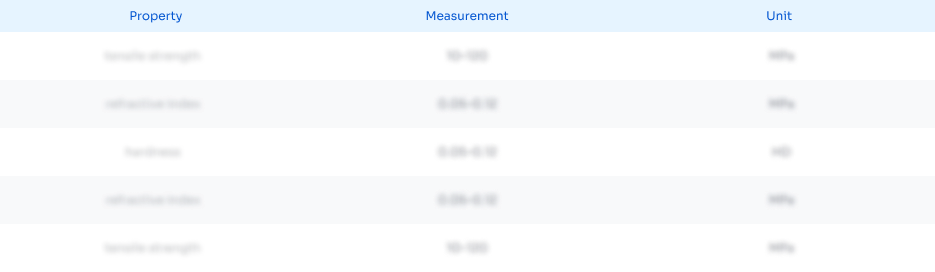
Abstract
Description
Claims
Application Information

- R&D Engineer
- R&D Manager
- IP Professional
- Industry Leading Data Capabilities
- Powerful AI technology
- Patent DNA Extraction
Browse by: Latest US Patents, China's latest patents, Technical Efficacy Thesaurus, Application Domain, Technology Topic, Popular Technical Reports.
© 2024 PatSnap. All rights reserved.Legal|Privacy policy|Modern Slavery Act Transparency Statement|Sitemap|About US| Contact US: help@patsnap.com