Automatic sand core taking and repairing mechanism
An automatic, sand-core technology, applied in the field of foundry repair, can solve the problems of increased production cost, long time consumption, waste of production waiting, etc.
- Summary
- Abstract
- Description
- Claims
- Application Information
AI Technical Summary
Problems solved by technology
Method used
Image
Examples
Embodiment Construction
[0015] The following will clearly and completely describe the technical solutions in the embodiments of the present invention with reference to the accompanying drawings in the embodiments of the present invention. Obviously, the described embodiments are only some, not all, embodiments of the present invention. Based on the embodiments of the present invention, all other embodiments obtained by persons of ordinary skill in the art without making creative efforts belong to the protection scope of the present invention.
[0016] see Figure 1-3 , the present invention provides a technical solution: an automatic sand core repair mechanism, including a bottom plate 1, positioning pillars 2 are fixedly installed at the four corners of the top of the bottom plate 1, a positioning sleeve 5 is fixedly installed on the top of the positioning pillar 2, and the top of the bottom plate 1 The middle part of one side is fixedly equipped with a positioning sleeve 9, and one side of the posi...
PUM
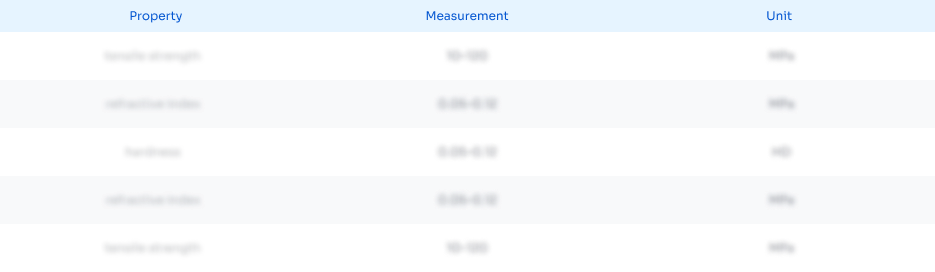
Abstract
Description
Claims
Application Information

- R&D
- Intellectual Property
- Life Sciences
- Materials
- Tech Scout
- Unparalleled Data Quality
- Higher Quality Content
- 60% Fewer Hallucinations
Browse by: Latest US Patents, China's latest patents, Technical Efficacy Thesaurus, Application Domain, Technology Topic, Popular Technical Reports.
© 2025 PatSnap. All rights reserved.Legal|Privacy policy|Modern Slavery Act Transparency Statement|Sitemap|About US| Contact US: help@patsnap.com