Robot motion error in-situ detection and compensation method and equipment
A technology of robot motion and detection method, applied in the directions of manipulators, program-controlled manipulators, manufacturing tools, etc., can solve the problems of large motion errors of robots, and achieve the effect of improving motion accuracy and convenient operation
- Summary
- Abstract
- Description
- Claims
- Application Information
AI Technical Summary
Problems solved by technology
Method used
Image
Examples
Embodiment 1
[0040] Such as figure 1 Shown is a schematic diagram of a device with a robot motion error detection and compensation function. Embodiment 1 of the present invention provides a robot with a robot motion error detection and compensation function. The device includes a robot body 1, Robot controller 2, process system 3, high-precision standard parts 5 and measuring device 4; measuring device 4 is installed at the end of robot body 1, and is electrically connected with process system 3 to realize motion error data transmission; robot controller 2 and robot body 1 , The process system 3 is electrically connected to realize program and signal transmission.
[0041] Such as figure 2 Shown is a flow chart of a robot motion error in-position detection method in the first embodiment of the present invention. A robot motion error in-position detection method in the first embodiment of the present invention includes the following steps:
[0042] Step S10: Based on the structural para...
Embodiment 2
[0067] Such as Figure 5 Shown is a flow chart of a robot motion error in-position compensation method in the second embodiment of the present invention. A robot motion error in-position compensation method in the second embodiment of the present invention includes the following steps:
[0068] Step S100: Obtain the first motion error of the robot at each sampling point by using any robot motion error in-position detection method in Embodiment 1;
[0069] Step S200: Compensate the motion error of the robot at each sampling point to the target motion trajectory to obtain the compensated motion trajectory.
[0070] Optionally, in order to verify the correctness of the robot motion error in-position compensation method in Embodiment 2 of the present invention, the following steps are also included:
[0071] Step S300: The robot makes the measuring device 4 move along the compensation trajectory. During the process of the robot moving the measuring device 4 along the compensation...
PUM
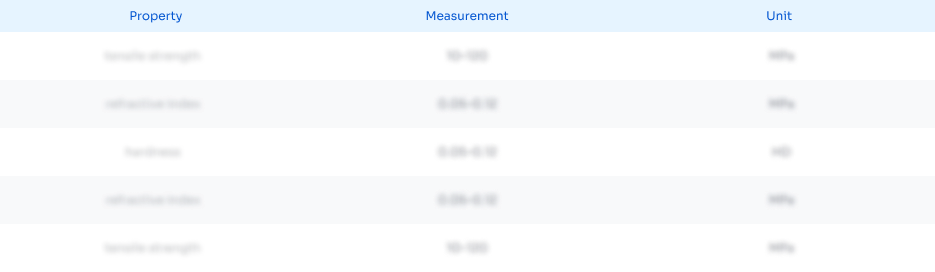
Abstract
Description
Claims
Application Information

- R&D
- Intellectual Property
- Life Sciences
- Materials
- Tech Scout
- Unparalleled Data Quality
- Higher Quality Content
- 60% Fewer Hallucinations
Browse by: Latest US Patents, China's latest patents, Technical Efficacy Thesaurus, Application Domain, Technology Topic, Popular Technical Reports.
© 2025 PatSnap. All rights reserved.Legal|Privacy policy|Modern Slavery Act Transparency Statement|Sitemap|About US| Contact US: help@patsnap.com