Ball joint pneumatic locking type rigidity-variable soft body arm framework
A technology of pneumatic locking and ball joints, applied in manipulators, program-controlled manipulators, manufacturing tools, etc., can solve problems such as the inability to realize motion control and environmental interaction functions at the same time, and the inability to adjust the stiffness of the manipulator
- Summary
- Abstract
- Description
- Claims
- Application Information
AI Technical Summary
Problems solved by technology
Method used
Image
Examples
Embodiment Construction
[0027] The present invention will be further described below in conjunction with the accompanying drawings and specific embodiments.
[0028] Such as Figure 1-5 In the shown embodiment, a ball joint pneumatic locking type variable stiffness soft arm skeleton includes a closed joint 1 at one end and several rotating assemblies connected in sequence, and the rotating assembly includes an outer shaft joint 2 and an inner shaft joint 3. The closed joint is connected to the outer shaft joint of one of the rotating assemblies, and the outer shaft joint of the rotating assembly is sleeved on the inner shaft joint of the adjacent rotating assembly, and the gap between the outer shaft joint and the inner shaft joint is Connected by a ball joint 4, the outer shaft joint includes two outer shaft joint connecting parts 21 respectively located on both sides of the ball joint, and the ball joint is provided with two outer shaft joint rotating shafts that are rotationally connected with the...
PUM
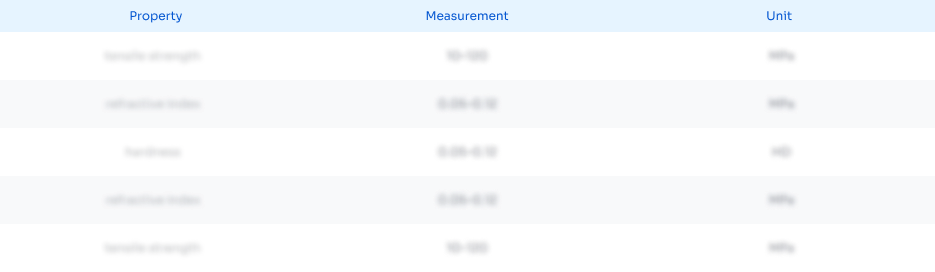
Abstract
Description
Claims
Application Information

- R&D
- Intellectual Property
- Life Sciences
- Materials
- Tech Scout
- Unparalleled Data Quality
- Higher Quality Content
- 60% Fewer Hallucinations
Browse by: Latest US Patents, China's latest patents, Technical Efficacy Thesaurus, Application Domain, Technology Topic, Popular Technical Reports.
© 2025 PatSnap. All rights reserved.Legal|Privacy policy|Modern Slavery Act Transparency Statement|Sitemap|About US| Contact US: help@patsnap.com