Multi-dimensional collaborative design method for multi-stage axial flow compressor of ship gas turbine
A technology for axial flow compressors and gas turbines, applied in computer-aided design, design optimization/simulation, calculation, etc., to achieve the effects of improving design accuracy, improving design efficiency, and shortening the design cycle
- Summary
- Abstract
- Description
- Claims
- Application Information
AI Technical Summary
Problems solved by technology
Method used
Image
Examples
Embodiment Construction
[0039] The present invention is described in more detail below in conjunction with accompanying drawing example:
[0040] combine figure 1 , a multi-dimensional collaborative design method for a multi-stage axial flow compressor of a marine gas turbine in the present invention is realized through the following steps:
[0041]Step 1: One-dimensional design and analysis link. Mainly carry out the one-dimensional inverse problem flow design and the one-dimensional forward problem characteristic calculation and analysis of the multi-stage axial flow compressor of the marine gas turbine. Among them, the one-dimensional inverse problem flow design is mainly through the design conditions (speed, stage pressure ratio, flow rate), inlet and outlet airflow conditions (inlet total pressure, total temperature, inlet and outlet airflow angle, inlet and outlet axial velocity) and some geometric conditions (Flow form, given flow channel outer diameter, axial clearance, etc.) are input to c...
PUM
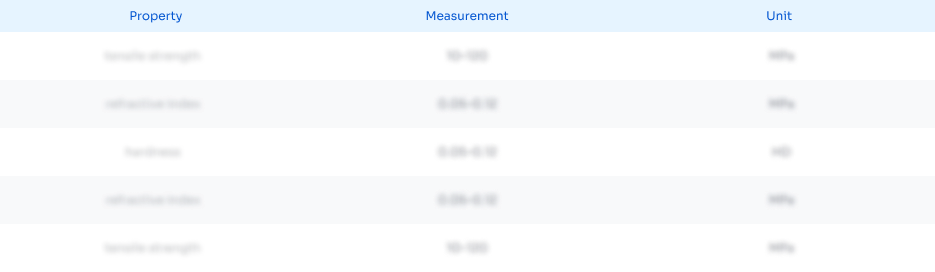
Abstract
Description
Claims
Application Information

- R&D Engineer
- R&D Manager
- IP Professional
- Industry Leading Data Capabilities
- Powerful AI technology
- Patent DNA Extraction
Browse by: Latest US Patents, China's latest patents, Technical Efficacy Thesaurus, Application Domain, Technology Topic, Popular Technical Reports.
© 2024 PatSnap. All rights reserved.Legal|Privacy policy|Modern Slavery Act Transparency Statement|Sitemap|About US| Contact US: help@patsnap.com