Rapid machine adjusting method and system for pipe bending machine
A pipe bending machine, fast technology, applied in image data processing, measuring devices, 3D modeling, etc., can solve problems such as inability to provide correction amount, high cost, and non-compliance with sustainable development strategies
- Summary
- Abstract
- Description
- Claims
- Application Information
AI Technical Summary
Problems solved by technology
Method used
Image
Examples
Embodiment Construction
[0078] like figure 2 As shown, a quick adjustment method of a pipe bending machine specifically includes the following steps:
[0079] S1. Select a multi-camera system;
[0080] S2. Establishing a model of internal and external parameters of the multi-camera system;
[0081] S3. Using the internal and external parameter models of the multi-camera system and using a calibration board to calibrate the multi-camera system;
[0082] S4. Use the calibrated multi-camera system to capture the image of the tube, and fit the seed cylinder;
[0083] S5. Using the seed cylinder as a reference, combined with the image of the pipe captured by the multi-camera system, retrieve and reconstruct the three-dimensional model of the pipe;
[0084] S6. Using the three-dimensional model of the pipe fitting to correct the size of the pipe bender.
[0085] A quick machine adjustment system for a pipe bender, comprising:
[0086] Multi-camera system: used to capture images of pipe fittings;
[...
PUM
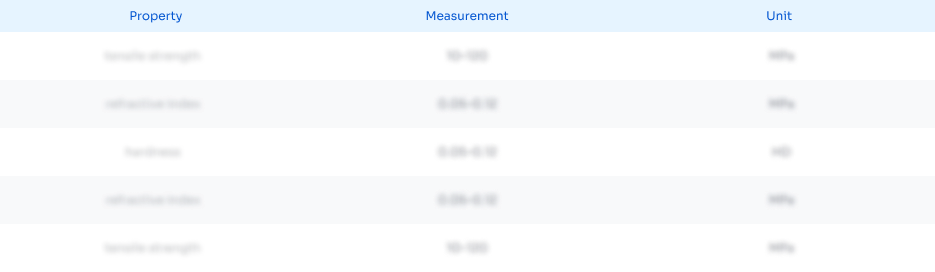
Abstract
Description
Claims
Application Information

- R&D Engineer
- R&D Manager
- IP Professional
- Industry Leading Data Capabilities
- Powerful AI technology
- Patent DNA Extraction
Browse by: Latest US Patents, China's latest patents, Technical Efficacy Thesaurus, Application Domain, Technology Topic, Popular Technical Reports.
© 2024 PatSnap. All rights reserved.Legal|Privacy policy|Modern Slavery Act Transparency Statement|Sitemap|About US| Contact US: help@patsnap.com