Bearing or thrust hobbing gear capable of achieving automatic clearance adjustment
An automatic adjustment and automatic adjustment technology, which is applied in the field of material mechanics and mechanics, can solve the problems of clearance or clearance reduction, changes in use conditions, and short life of workpieces.
- Summary
- Abstract
- Description
- Claims
- Application Information
AI Technical Summary
Problems solved by technology
Method used
Image
Examples
Embodiment Construction
[0055] Preferred embodiments of the present invention will be described with reference to the drawings.
[0056] figure 1 It is a schematic diagram of the friction body support part as an independent part, and the deformation of the support part under the action of the automatic adjustment device leads to the change of the clearance. Picture 1-1 is before deformation, Figure 1-2 After deformation. Depend on Picture 1-1 It can be seen that the deformable friction body supporting part b1 supports the friction body a, so that the friction body is close to the direction of the friction surface body, compared with Figure 1-2 It can be seen that when the automatic adjustment device c expands to the left and right, the friction body support part b1 deforms to keep the friction body away from the friction surface; conversely, when the automatic adjustment device c shortens, the friction body deforms in the opposite direction.
[0057] figure 2 It is a schematic diagram of th...
PUM
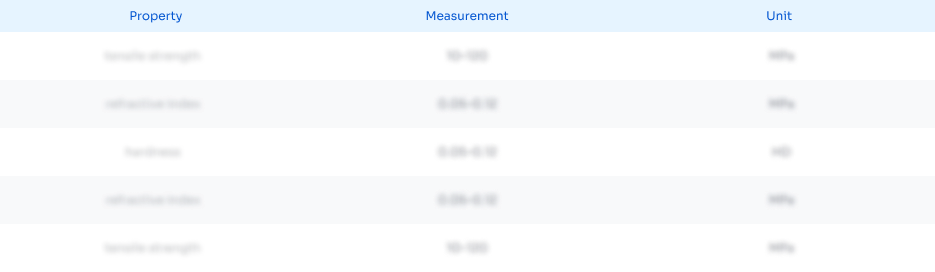
Abstract
Description
Claims
Application Information

- R&D
- Intellectual Property
- Life Sciences
- Materials
- Tech Scout
- Unparalleled Data Quality
- Higher Quality Content
- 60% Fewer Hallucinations
Browse by: Latest US Patents, China's latest patents, Technical Efficacy Thesaurus, Application Domain, Technology Topic, Popular Technical Reports.
© 2025 PatSnap. All rights reserved.Legal|Privacy policy|Modern Slavery Act Transparency Statement|Sitemap|About US| Contact US: help@patsnap.com