Silk thread winding roller for textile machinery
A technology for textile machinery and winding rollers, which is applied in the field of silk winding rollers for textile machinery, which can solve the problems of waste of manpower, inconsistent rotation of cylinder rollers, interweaving, etc., and achieve the effects of improving use efficiency, production efficiency, and production efficiency
- Summary
- Abstract
- Description
- Claims
- Application Information
AI Technical Summary
Problems solved by technology
Method used
Image
Examples
Embodiment 1
[0030] see Figure 1-7 , the present invention provides a technical solution: a silk winding roller for textile machinery, comprising a first fixed rod 1, a second fixed rod 26 and a roller cylinder 29, one end of the first fixed rod 1 is fixedly mounted with two first The limit hinge plate 2, the inner side of the other end of the two first limit hinge plates 2 is plugged with the first latch shaft 12, the outer side of the first latch shaft 12 is inserted with the second limit hinge plate 3, the second limit hinge plate 3 One end of the hinge plate 3 away from the first latch shaft 12 is fixedly installed with a connecting shaft 16, and the other end of the connecting shaft 16 is fixedly installed with a second limiting plate 11, and the side of the second limiting plate 11 away from the connecting shaft 16 is fixedly installed. There is a rotating electrical machine 4, and the other end of the rotating electrical machine 4 is fixedly installed with a first limiting plate 10...
Embodiment 2
[0033] like Figure 1-7 As shown, on the basis of Embodiment 1, the present invention provides a technical solution: the dimensions of the ball post 34 are compatible with the dimensions of the ball retaining groove 32, and the dimensions of the roller clamp 33 are compatible with the dimensions of the roller clamp. The dimensions of the slot 35 are compatible, the dimensions of the four bayonets 8 are compatible with the dimensions of the four buckles 30, and the positions of the four bayonets 8 and the four buckles 30 are corresponding. The size specification of 19 is compatible with the size specification of the limit hole 36, and the position of the limit rod 19 is corresponding to the position of the limit hole 36.
[0034] In this embodiment, by providing bayonet 8 and buckle 30, when the roller cylinder 29 is replaced, the side of the roller cylinder 29 installed with the first limit ring plate 31 can be sleeved into the outside of the roller column 7, and The buckle 3...
Embodiment 3
[0036] like Figure 1-7 As shown, on the basis of Embodiment 1 and Embodiment 2, the present invention provides a technical solution: a first limit ring plate 31 is fixedly installed on one end of the roller cylinder 29, and the first limit ring plate 31 is far away from the roller One side of the cylinder 29 is fixedly equipped with four buckles 30, and the other end of the roller cylinder 29 is fixedly equipped with a second spacer ring plate 37, and the side of the second spacer circle plate 37 away from the roller cylinder 29 is provided with a Two limiting holes 36, the outer side of the roller cylinder 29 is provided with a roller clamping groove 35, and the bottom of the roller clamping groove 35 is provided with a parking ball clamping groove 32, and the roller cylinder clamping groove 35 is away from the side of the parking ball clamping groove 32 The side wall of the side wall is hinged with a roller clamp 33, and the bottom of the roller clamp 33 is fixedly equipped...
PUM
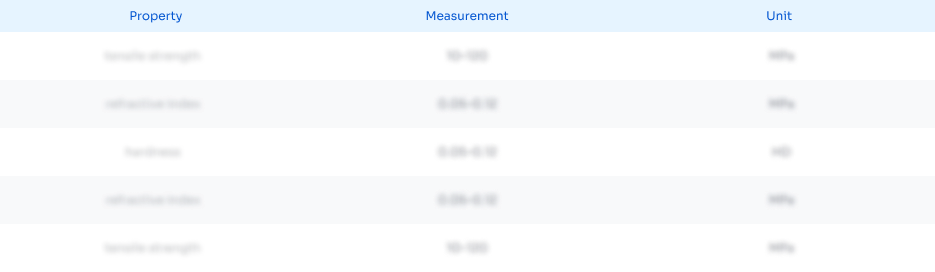
Abstract
Description
Claims
Application Information

- Generate Ideas
- Intellectual Property
- Life Sciences
- Materials
- Tech Scout
- Unparalleled Data Quality
- Higher Quality Content
- 60% Fewer Hallucinations
Browse by: Latest US Patents, China's latest patents, Technical Efficacy Thesaurus, Application Domain, Technology Topic, Popular Technical Reports.
© 2025 PatSnap. All rights reserved.Legal|Privacy policy|Modern Slavery Act Transparency Statement|Sitemap|About US| Contact US: help@patsnap.com