A wire-actuated joint that enables decoupling of bending motion
A bending motion and joint technology, applied in the field of robotics, can solve problems such as increasing control difficulty
- Summary
- Abstract
- Description
- Claims
- Application Information
AI Technical Summary
Problems solved by technology
Method used
Image
Examples
Embodiment 1
[0033] like figure 1 As shown, this embodiment provides a wire-driven joint capable of decoupling bending motion, including a base plate 1, a connecting rod 2, an end plate 3, a first wire and a second wire; the base plate 1 and The connecting rod 2 is connected to form a first rotating pair 8, and the rotation axis of the first rotating pair 8 coincides with the end surface of the base plate 1; the end plate 3 is connected to the connecting rod 2 to form a second Two rotating pairs 9, the rotation axis of the second rotating pair 9 coincides with the end surface of the end disk 3; one end of the first wire is fixedly connected to the end disk 3, and the other end passes through the end disk 3, The connecting rod 2, the first rotating pair 8 and the base plate 1; one end of the second wire is fixedly connected to the end plate 3, and the other end passes through the end plate 3, the second rotating pair 9, the connecting rod 2 and the Base plate 1.
[0034]In this embodiment...
Embodiment 2
[0042] like figure 1 As shown, this embodiment provides a wire-driven joint capable of decoupling bending motion, including a base plate 1, a connecting rod 2, an end plate 3, a first wire and a second wire; the base plate 1 and The connecting rod 2 is connected to form a first rotating pair 8, and the rotation axis of the first rotating pair 8 coincides with the end surface of the base plate 1; the end plate 3 is connected to the connecting rod 2 to form a second Two rotating pairs 9, the rotation axis of the second rotating pair 9 coincides with the end surface of the end disk 3; one end of the first wire is fixedly connected to the end disk 3, and the other end passes through the end disk 3, The connecting rod 2, the first rotating pair 8 and the base plate 1; one end of the second wire is fixedly connected to the end plate 3, and the other end passes through the end plate 3, the second rotating pair 9, the connecting rod 2 and the Base plate 1.
[0043] like Figure 3-5...
PUM
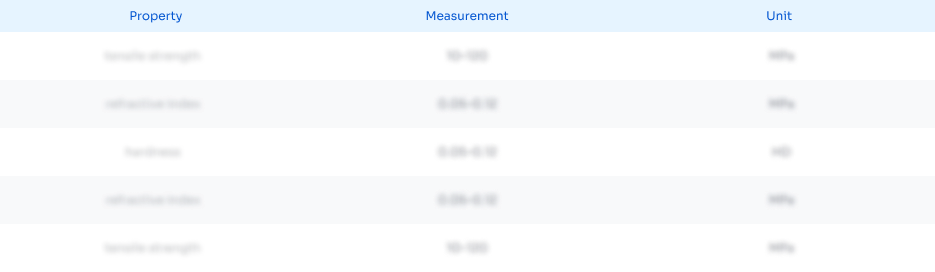
Abstract
Description
Claims
Application Information

- R&D
- Intellectual Property
- Life Sciences
- Materials
- Tech Scout
- Unparalleled Data Quality
- Higher Quality Content
- 60% Fewer Hallucinations
Browse by: Latest US Patents, China's latest patents, Technical Efficacy Thesaurus, Application Domain, Technology Topic, Popular Technical Reports.
© 2025 PatSnap. All rights reserved.Legal|Privacy policy|Modern Slavery Act Transparency Statement|Sitemap|About US| Contact US: help@patsnap.com