Track robot positioning calibration device and calibration method
A technology of orbital robot and calibration device, applied in the direction of cooperating devices, instruments, computer parts, etc., can solve the problems of large sensing distance, inability to achieve positioning, single sensing method, etc., and achieve the effect of accurate calibration.
- Summary
- Abstract
- Description
- Claims
- Application Information
AI Technical Summary
Problems solved by technology
Method used
Image
Examples
Embodiment Construction
[0015] The present invention will be described in further detail below in conjunction with the accompanying drawings.
[0016] Such as figure 1 Shown, a kind of rail robot positioning calibration device comprises an RFID tag 1 and two magnetic nails 2, and RFID is installed between two magnetic nails 2, and the distance between each magnetic nail 2 and RFID tag 1 is at least 30cm; A non-contact RFID antenna and a Hall induction device for inducting the RFID tag 1 and the magnetic nail 2 are installed on the track robot.
[0017] Further, the magnetic nail 2 is inserted into the track 3 and fixed by the plastic magnetic nail 2 holder.
[0018] Further, the RFID tag is connected and fixed to the track 3 through a bracket.
[0019] A method for positioning and calibrating an orbital robot of the present invention comprises the following steps:
[0020] (1) Install and fix the RFID tag and a magnetic nail 2 on both sides thereof on the robot track 3, and set the initial positio...
PUM
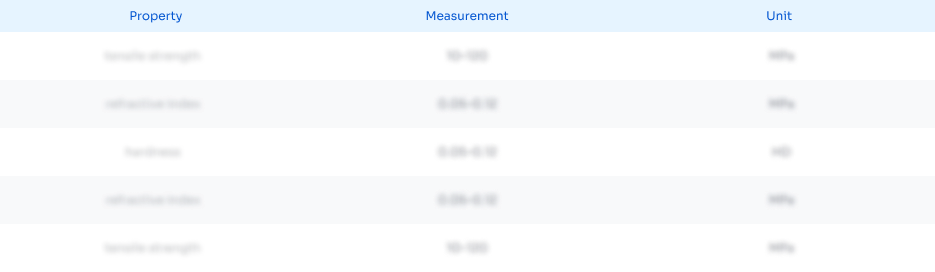
Abstract
Description
Claims
Application Information

- Generate Ideas
- Intellectual Property
- Life Sciences
- Materials
- Tech Scout
- Unparalleled Data Quality
- Higher Quality Content
- 60% Fewer Hallucinations
Browse by: Latest US Patents, China's latest patents, Technical Efficacy Thesaurus, Application Domain, Technology Topic, Popular Technical Reports.
© 2025 PatSnap. All rights reserved.Legal|Privacy policy|Modern Slavery Act Transparency Statement|Sitemap|About US| Contact US: help@patsnap.com