A High-Precision Dynamic Measuring Method of Tension in Damping Suspension Rod System
A high-precision, boom-based technology, applied in force/torque/power measuring instruments, measuring devices, instruments, etc., can solve problems such as insufficient precision, and achieve the effect of increasing the matrix condition number, increasing the condition number, and increasing stability
- Summary
- Abstract
- Description
- Claims
- Application Information
AI Technical Summary
Problems solved by technology
Method used
Image
Examples
Embodiment
[0184]The application of this method is illustrated below in conjunction with the examples, and compared with the practical formula method proposed by Zui et al. (1996). The practical formula proposed by Zui et al. (1996) is as follows:
[0185]
[0186] in:
[0187] In this embodiment, the problem of force measurement by vibration method of two actual arch bridge suspenders is discussed. The boom is composed of 91 steel wires with a diameter of 7mm. The elastic modulus of the steel wire is 1.95e+005MPa, the mass per unit length of the boom is 27.48kg / m, and the cross-sectional area of the boom is 0.0035mm 2 . Table 1 gives the mechanical parameters of two booms, one of which is a short boom (2.34m) and the other is a long boom (10.2m). The boundary rotation and lateral stiffness of the boom are respectively 12EI / l and 48EI / l 3 . The stiffness and damping values of the damper are selected according to the normal range. At this time, the short boom and long boom ...
PUM
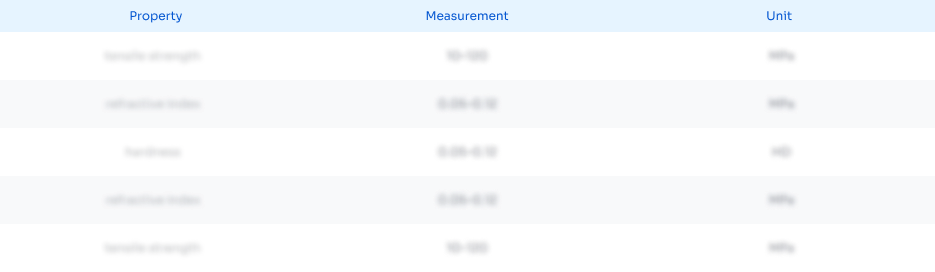
Abstract
Description
Claims
Application Information

- R&D
- Intellectual Property
- Life Sciences
- Materials
- Tech Scout
- Unparalleled Data Quality
- Higher Quality Content
- 60% Fewer Hallucinations
Browse by: Latest US Patents, China's latest patents, Technical Efficacy Thesaurus, Application Domain, Technology Topic, Popular Technical Reports.
© 2025 PatSnap. All rights reserved.Legal|Privacy policy|Modern Slavery Act Transparency Statement|Sitemap|About US| Contact US: help@patsnap.com