General assembly workshop repair area exhaust fan control management system and method
A technology for assembly workshop and control management, which is applied in the field of control systems, can solve the problems of overuse, waste, and unsatisfactory effects of fans, and achieve the effects of saving man-hour costs, energy waste, and rich functions
- Summary
- Abstract
- Description
- Claims
- Application Information
AI Technical Summary
Problems solved by technology
Method used
Image
Examples
Embodiment Construction
[0031] In order to make the object, technical solution and effect of the present invention more clear and definite, the present invention will be further described in detail below with reference to the accompanying drawings and examples. It should be understood that the specific embodiments described here are only used to explain the present invention, not to limit the present invention.
[0032] Please also refer to Figure 1-Figure 5 , the present invention provides a control and management system for exhaust fans in the rework area of an assembly workshop, including a main gate control device 1, a plurality of branch gate control devices 2 and a plurality of fan switch controllers 3;
[0033] The main gate control device 1 comprises a main gate power supply 11, a PLC (Programmable Logic Controller, programmable logic controller) controller 12 and a switch 13; Power supply, the PLC controller 12 sends control signals to the opening control device 2 through the switch 13; ...
PUM
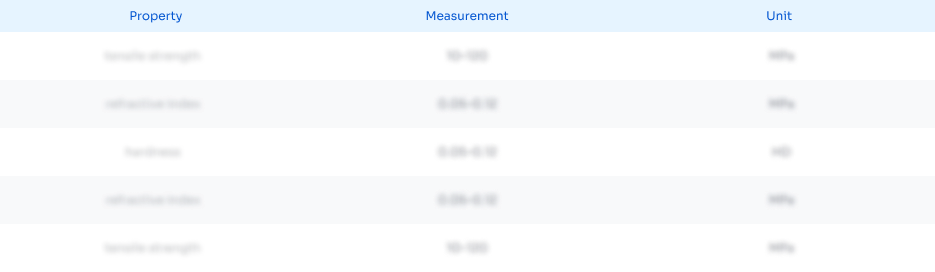
Abstract
Description
Claims
Application Information

- R&D Engineer
- R&D Manager
- IP Professional
- Industry Leading Data Capabilities
- Powerful AI technology
- Patent DNA Extraction
Browse by: Latest US Patents, China's latest patents, Technical Efficacy Thesaurus, Application Domain, Technology Topic, Popular Technical Reports.
© 2024 PatSnap. All rights reserved.Legal|Privacy policy|Modern Slavery Act Transparency Statement|Sitemap|About US| Contact US: help@patsnap.com