Calibration method of non-orthogonal nonlinear 3D scanning probe under cylindrical coordinate measuring machine
A cylindrical coordinate, three-dimensional scanning technology, applied in the field of precision measurement, can solve the problems of many calibration parameters and difficult to optimize, and achieve the effect of wide applicability
- Summary
- Abstract
- Description
- Claims
- Application Information
AI Technical Summary
Problems solved by technology
Method used
Image
Examples
Embodiment Construction
[0048] The present invention will be further described below in conjunction with specific drawings and embodiments.
[0049] The embodiment of the present invention proposes a method for calibrating a non-orthogonal nonlinear three-dimensional scanning probe under a cylindrical coordinate measuring machine, which includes the following steps:
[0050] Step one, such as figure 1 As shown, three axes are defined on the cylindrical coordinate measuring machine, including two translation axes X-axis and Z-axis, and one rotation axis C-axis (that is, the rotation axis of the turntable); and a coordinate system is established accordingly;
[0051] Establish the machine coordinate system W of the cylindrical coordinate measuring machine M and the probe coordinate system W of the probe on the cylindrical coordinate measuring machine T ;The machine coordinate system takes the zero position of the cylindrical coordinate measuring machine as the coordinate origin, and the probe coordin...
PUM
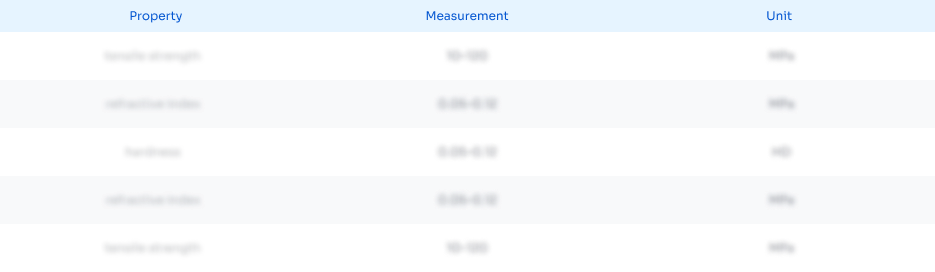
Abstract
Description
Claims
Application Information

- R&D
- Intellectual Property
- Life Sciences
- Materials
- Tech Scout
- Unparalleled Data Quality
- Higher Quality Content
- 60% Fewer Hallucinations
Browse by: Latest US Patents, China's latest patents, Technical Efficacy Thesaurus, Application Domain, Technology Topic, Popular Technical Reports.
© 2025 PatSnap. All rights reserved.Legal|Privacy policy|Modern Slavery Act Transparency Statement|Sitemap|About US| Contact US: help@patsnap.com