Active load reduction structure of aircraft
A technology of active load reduction and aircraft, applied in the direction of motor vehicles, hydrodynamic characteristics/hydrostatic characteristics, underwater operation equipment, etc., can solve problems such as unacceptable weight, space, and performance costs
- Summary
- Abstract
- Description
- Claims
- Application Information
AI Technical Summary
Problems solved by technology
Method used
Image
Examples
Embodiment Construction
[0023] Now in conjunction with embodiment, accompanying drawing, the present invention will be further described:
[0024] as attached figure 1 As shown, the application object of the present invention is an underwater vehicle. Generally, an underwater vehicle can be divided into a vehicle head 1 , a vehicle middle section 2 , and a vehicle tail section 3 . In the present invention, an active load reduction system is provided in the aircraft head 1, and the active load reduction system takes up less space and does not have a large impact on the overall layout. The active load reduction system includes a jet rectifier valve 4, a jet on-off valve 5 and a high-pressure gas cylinder 6. The jet rectifying valve 4 is installed in the very center of the aircraft head 1, and the jet rectifying valve 4 includes a plurality of evenly distributed flat-shaped jet holes, which can evenly inject air flow. The uniformity here includes not only the uniformity of the injection airflow betwe...
PUM
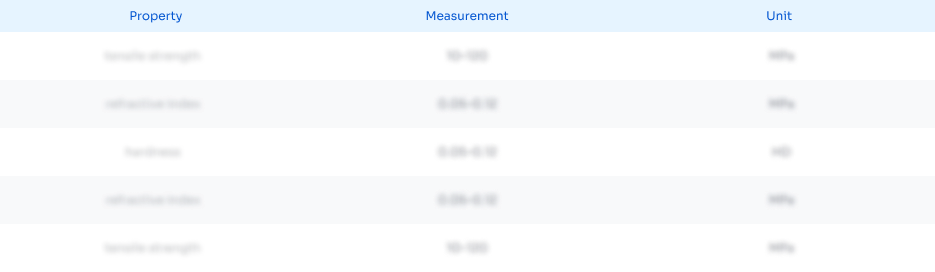
Abstract
Description
Claims
Application Information

- R&D
- Intellectual Property
- Life Sciences
- Materials
- Tech Scout
- Unparalleled Data Quality
- Higher Quality Content
- 60% Fewer Hallucinations
Browse by: Latest US Patents, China's latest patents, Technical Efficacy Thesaurus, Application Domain, Technology Topic, Popular Technical Reports.
© 2025 PatSnap. All rights reserved.Legal|Privacy policy|Modern Slavery Act Transparency Statement|Sitemap|About US| Contact US: help@patsnap.com