Mechanical clamping claw capable of stably grasping workpiece
A technology of mechanical gripper and workpiece, applied in the field of mechanical gripper, can solve the problems of difficult to grasp workpiece, easy to grasp unstable workpiece, etc., and achieve the effect of easy grasping and high elasticity
- Summary
- Abstract
- Description
- Claims
- Application Information
AI Technical Summary
Problems solved by technology
Method used
Image
Examples
Embodiment Construction
[0022] Such as figure 1 As shown, the mechanical jaws for stably grasping the workpiece include jaw main body 10, first jaw arm, second jaw arm, torsion arm 26, extension spring 30, motor, and the first jaw arm includes force arm 22, driven arm 21 , the second clamping arm includes a main arm 27 and an auxiliary arm 28 . The driven arm 21 and the force applying arm 22 are equipped with a third hinge shaft 41 and a second hinge shaft 40 respectively and are hinged on the left side in the jaw main body 10 through respective hinge shafts, and the proximal end of the main arm 27 is equipped with a second hinge shaft 40. A hinge 23 is also hinged on the right side in the jaw main body 10 by the first hinge 23; the proximal end of the auxiliary arm 28 is hinged on the housing of the jaw main body 10, and the hinge 25 of the two is as image 3 As shown, the hinge 25 is only on the housing and not through the jaw body 10 . The distal ends of the main arm 27 and the auxiliary arm 28 ...
PUM
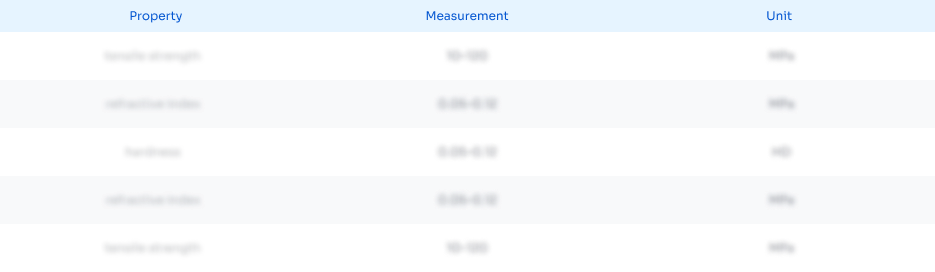
Abstract
Description
Claims
Application Information

- R&D
- Intellectual Property
- Life Sciences
- Materials
- Tech Scout
- Unparalleled Data Quality
- Higher Quality Content
- 60% Fewer Hallucinations
Browse by: Latest US Patents, China's latest patents, Technical Efficacy Thesaurus, Application Domain, Technology Topic, Popular Technical Reports.
© 2025 PatSnap. All rights reserved.Legal|Privacy policy|Modern Slavery Act Transparency Statement|Sitemap|About US| Contact US: help@patsnap.com