Forming tooling for a laminated unit body of a composite fan blade
A technology for forming tooling and fan blades, which is applied in the field of composite material manufacturing, can solve the problems of complex forming process, long layup cycle, and high requirements on the surface accuracy of parts with thickness changes from tenon to blade tip, so as to improve production efficiency and improve the surface. Quality, the effect of shortening the operation time
- Summary
- Abstract
- Description
- Claims
- Application Information
AI Technical Summary
Problems solved by technology
Method used
Image
Examples
Embodiment Construction
[0023] The technical scheme of the present invention will be described in further detail below in conjunction with accompanying drawing and embodiment:
[0024] See attached figure 1 , 2 As shown, the molding tooling of this kind of composite fan blade layup unit includes a layup platform 1 and a layup working surface 2 arranged on the layup platform 1, and layup datums are set on both sides of the layup working surface 2 Block 3 is used as a lay-up reference, and the number of lay-up working surfaces 2 is the same as the number of lay-up units in the tenon of the composite fan blade.
[0025] In this embodiment, the shape of the lay-up working surface 2 is center-symmetrical, and the two sides of the center point are the concave working surface 4 and the convex working surface 5 respectively, and the concave working surface 4 is used for the suction of the tenon of the composite fan blade. The suction surface layer unit body 6 on the surface side, the convex working surface...
PUM
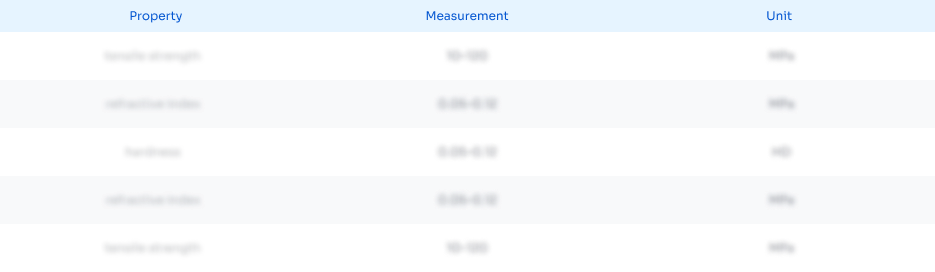
Abstract
Description
Claims
Application Information

- R&D
- Intellectual Property
- Life Sciences
- Materials
- Tech Scout
- Unparalleled Data Quality
- Higher Quality Content
- 60% Fewer Hallucinations
Browse by: Latest US Patents, China's latest patents, Technical Efficacy Thesaurus, Application Domain, Technology Topic, Popular Technical Reports.
© 2025 PatSnap. All rights reserved.Legal|Privacy policy|Modern Slavery Act Transparency Statement|Sitemap|About US| Contact US: help@patsnap.com