Socks production line and production method
A technology for production lines and socks, applied in textile and papermaking, fabric surface trimming, weft knitting, etc., can solve the problems of need to improve production efficiency, different setting tooling and process, low production efficiency, etc., and achieve fewer shutdowns for wiring. , high production efficiency, the effect of improving production efficiency
- Summary
- Abstract
- Description
- Claims
- Application Information
AI Technical Summary
Problems solved by technology
Method used
Image
Examples
Embodiment 1
[0068] Such as Figure 1-Figure 7 As shown, the sock production line provided in this embodiment includes sequentially connected batching area 100, weaving area 200, turnover area 300, shaping area 400, packaging area 500, and is used to control the weaving area 200, batching area 100, and shaping area. 400, the control module (not shown in the figure) of the working sequence of the turnover area 300 and the packaging area 500, wherein, the control module is a conventional module, such as a computer, which is not the focus of this embodiment, and can be purchased directly from the market and It is obtained by setting according to actual functional requirements, and will not be described in detail here.
[0069] Such as figure 1 and figure 2 As shown, the batching area 100 is provided with the batching conveyor line 110 connected to one end of the feeding conveyor line 210 (the feeding conveyor line 210 is arranged in the weaving zone 200, which will be described below), and...
Embodiment 2
[0088] This embodiment provides a sock production line. The difference between it and Embodiment 1 is that in this embodiment, the turnover area is canceled, and at the same time, an annular circular conveying line is used instead of the shaping conveying line in Embodiment 1. Specifically, this embodiment The shaping area in the example is provided with an annular circular conveying line and more than two branch conveying lines connected in parallel beside the circulating conveying line, each branch conveying line is equipped with a setting machine respectively, and the circulating conveying line is connected with each branch conveying line The position is respectively provided with a shaping steering device and a shaping identification component, and the circulating conveying line is connected with the feeding conveying line.
Embodiment 3
[0090] This embodiment provides a method for producing socks, using the socks production line provided in Embodiment 1 or Embodiment 2, refer to figure 1 , figure 2 and Figure 5 As shown, the method includes the following steps:
[0091] S1, batching, on the batching conveying line 110, place the same number of raw material boxes as the number of hosiery machines 220 in sequence, sort the yarn bobbins required for the production of each hosiery machine within a predetermined period of time into each raw material box in turn, and sequentially sort each raw material box, wherein the predetermined period of time is preferably one day, that is, one ingredient can meet the production needs of the socks production line for one day; the required yarn bobbins include the number and type of yarn bobbins, and the specific information can be manually imported into the control module. Or import it through other existing systems, such as EMS systems, etc.; the specific way of marking i...
PUM
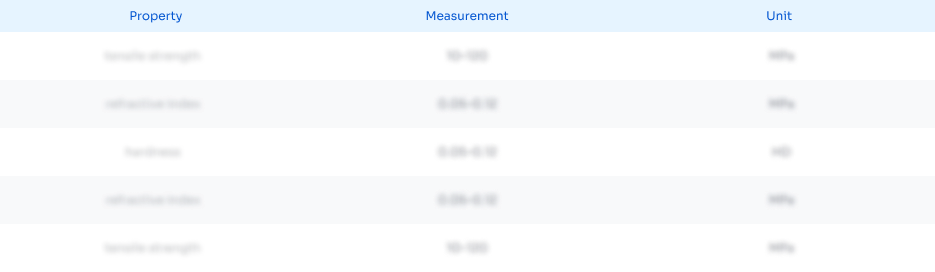
Abstract
Description
Claims
Application Information

- Generate Ideas
- Intellectual Property
- Life Sciences
- Materials
- Tech Scout
- Unparalleled Data Quality
- Higher Quality Content
- 60% Fewer Hallucinations
Browse by: Latest US Patents, China's latest patents, Technical Efficacy Thesaurus, Application Domain, Technology Topic, Popular Technical Reports.
© 2025 PatSnap. All rights reserved.Legal|Privacy policy|Modern Slavery Act Transparency Statement|Sitemap|About US| Contact US: help@patsnap.com