Different-direction stirring and mixing method for chemical raw materials
A chemical raw material, stirring and mixing technology, which is applied to mixers, chemical instruments and methods, and mixers with rotary stirring devices, can solve problems such as low efficiency, high energy consumption, and inability to carry out normal production, and achieves stirring. Better effect and less labor-intensive effect
- Summary
- Abstract
- Description
- Claims
- Application Information
AI Technical Summary
Problems solved by technology
Method used
Image
Examples
Embodiment Construction
[0063] The counter-rotating mixing method of chemical raw materials, the steps are:
[0064] S1: The operator puts the materials to be stirred into the mixing tank 100 in sequence;
[0065] S2: The counter-rotating mechanism 300 starts to operate;
[0066] The stirring tank 100 is vertically installed on the main frame body 210 of the automatic dumping mechanism 200, the different direction stirring mechanism 300 is installed on the main frame body 210 and the different direction stirring mechanism 300 is coaxially located in the stirring tank 100, and the different direction stirring mechanism The mechanism 300 includes a connecting bracket 310, a stirring member 320, and a driving member 330, and the connecting bracket 310 is fixedly installed on the mounting bracket 215;
[0067] The stirring member 320 includes an inner ring stirring member 3210 and an outer ring stirring member 3220;
[0068] The inner ring stirring member 3210 includes a rotating shaft 3211, a traction...
PUM
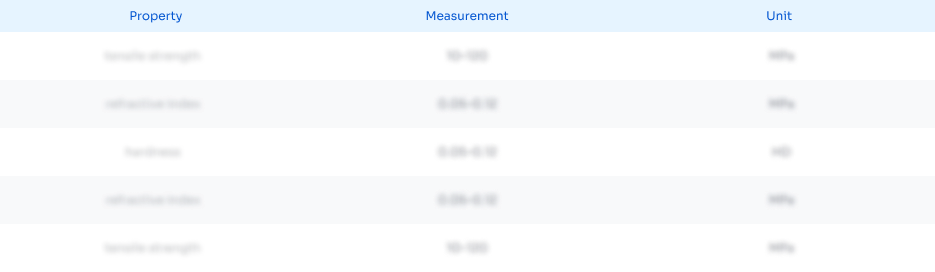
Abstract
Description
Claims
Application Information

- Generate Ideas
- Intellectual Property
- Life Sciences
- Materials
- Tech Scout
- Unparalleled Data Quality
- Higher Quality Content
- 60% Fewer Hallucinations
Browse by: Latest US Patents, China's latest patents, Technical Efficacy Thesaurus, Application Domain, Technology Topic, Popular Technical Reports.
© 2025 PatSnap. All rights reserved.Legal|Privacy policy|Modern Slavery Act Transparency Statement|Sitemap|About US| Contact US: help@patsnap.com