Experimental method for simulating variable load and variable inertia of industrial robot joints
An industrial robot and experimental method technology, applied in the field of joint servo control system testing, can solve the problems of large hydraulic source, mechanical load that cannot simulate continuous load spectrum, and load that cannot be changed or adjusted during operation
- Summary
- Abstract
- Description
- Claims
- Application Information
AI Technical Summary
Problems solved by technology
Method used
Image
Examples
Embodiment Construction
[0042] The present invention will be further described below in conjunction with accompanying drawing:
[0043] Such as Figure 1-8 As shown, an experimental method for simulating the variable load and variable inertia of the industrial robot joints adopts the experimental device for simulating the variable load and variable inertia of the industrial robot joints. Circuit, dynamometer controller, working table 17, input servo motor 1, planetary gear reducer 2, first coupling 3, dynamic torque sensor 4, second coupling 5, angle sensor 6, double bearing housing 7 , variable inertia lever arm 9, third coupling 12, rotating shaft 11, mass slider 8, positioning bolt 10, hysteresis dynamometer 13, first support base 14, second support base 15 and third support base 16 , the input servo motor 1 and the planetary gear reducer 2 are fixed on the third support base 16, and the output shaft of the input servo motor 1 is sequentially connected to the planetary gear reducer 2 and the firs...
PUM
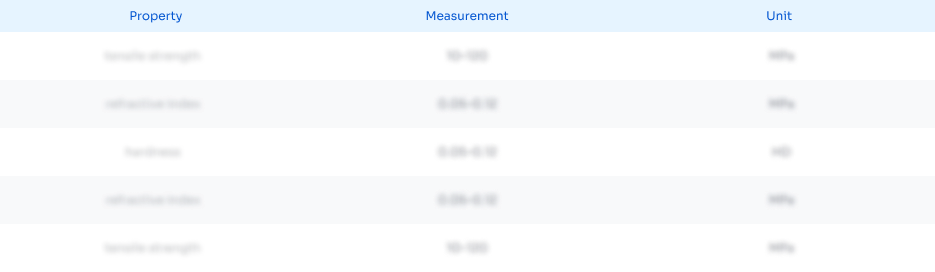
Abstract
Description
Claims
Application Information

- R&D
- Intellectual Property
- Life Sciences
- Materials
- Tech Scout
- Unparalleled Data Quality
- Higher Quality Content
- 60% Fewer Hallucinations
Browse by: Latest US Patents, China's latest patents, Technical Efficacy Thesaurus, Application Domain, Technology Topic, Popular Technical Reports.
© 2025 PatSnap. All rights reserved.Legal|Privacy policy|Modern Slavery Act Transparency Statement|Sitemap|About US| Contact US: help@patsnap.com