Calibration method and calibration device of multi-shaft force sensor
A multi-axis force sensor and sensor technology, applied in the direction of force/torque/power measuring instrument calibration/testing, measuring devices, instruments, etc., can solve problems such as heavy workload, interference, installation error, etc., and reduce the adjustment workload , The device is convenient and effective, and the effect of improved accuracy
- Summary
- Abstract
- Description
- Claims
- Application Information
AI Technical Summary
Problems solved by technology
Method used
Image
Examples
Embodiment Construction
[0051] The present invention mainly aims at the problem of insufficient installation and positioning accuracy in the current multi-axis force sensor calibration process, and provides an installation method for adjusting the attitude, which can keep the installation states of different sensors consistent, thereby eliminating the problems caused by differences in the installation states of the sensors. Error, improve the calibration accuracy of the sensor. The specific implementation manners of the present invention will be further described in detail below in conjunction with the accompanying drawings.
[0052] An installation and positioning method used in the calibration process of a multi-axis force sensor, the schematic diagram of the multi-axis force sensor installed on the calibration table is shown in the attached figure 1 As shown, the main components include a support mechanism 1, a multi-axis force sensor 2, a loading plate 3, a steel wire 4 connecting the loading pla...
PUM
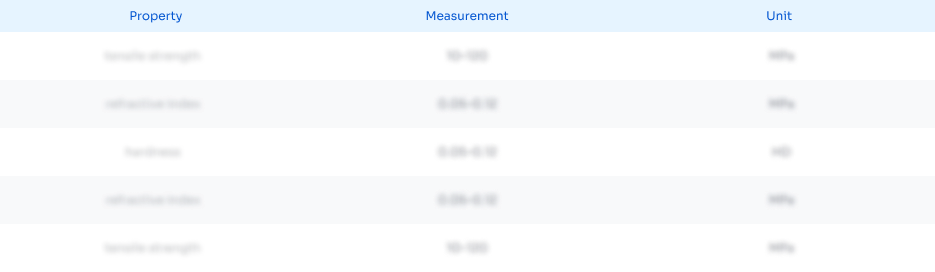
Abstract
Description
Claims
Application Information

- R&D
- Intellectual Property
- Life Sciences
- Materials
- Tech Scout
- Unparalleled Data Quality
- Higher Quality Content
- 60% Fewer Hallucinations
Browse by: Latest US Patents, China's latest patents, Technical Efficacy Thesaurus, Application Domain, Technology Topic, Popular Technical Reports.
© 2025 PatSnap. All rights reserved.Legal|Privacy policy|Modern Slavery Act Transparency Statement|Sitemap|About US| Contact US: help@patsnap.com