Outdoor live working robot mechanical arm capable of automatically switching tools
A technology of live working and robotics, which is applied in the direction of manipulators, manufacturing tools, and program-controlled manipulators. It can solve the problems of damaged manipulators, affecting work efficiency, and slow work, and achieves efficient control, improved work efficiency, and convenient operation.
- Summary
- Abstract
- Description
- Claims
- Application Information
AI Technical Summary
Problems solved by technology
Method used
Image
Examples
specific Embodiment approach
[0044] When working outdoors, the robot realizes multi-degree-of-freedom activities between the mechanical arm 1, the small arm 2 and the mechanical forearm through the joint drive (generally, the dual mechanical arms are used to cooperate with live work), and different live working tool components are realized through the mechanical forearm. The docking, grasping and driving operations can be carried out independently, so as to independently complete the operations of live disconnection, live connection, live replacement of lightning arresters, live replacement of isolating switches, live replacement of drop-out fuses, live replacement of insulating protective tubes, etc.
[0045] When the mechanical arm replaces the tool, firstly the mechanical forearm drives the original tool assembly to move to the front side of the tool position, and then horizontally translates to the top of the tool position, then descends and puts the original tool assembly into the tool position. At thi...
PUM
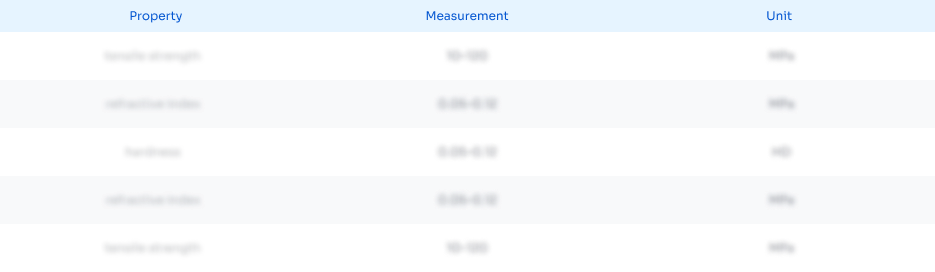
Abstract
Description
Claims
Application Information

- R&D
- Intellectual Property
- Life Sciences
- Materials
- Tech Scout
- Unparalleled Data Quality
- Higher Quality Content
- 60% Fewer Hallucinations
Browse by: Latest US Patents, China's latest patents, Technical Efficacy Thesaurus, Application Domain, Technology Topic, Popular Technical Reports.
© 2025 PatSnap. All rights reserved.Legal|Privacy policy|Modern Slavery Act Transparency Statement|Sitemap|About US| Contact US: help@patsnap.com