Shift management in model predictive based propulsion system control
A propulsion system and control system technology, applied in the direction of control devices, external condition input parameters, driver input parameters, etc.
- Summary
- Abstract
- Description
- Claims
- Application Information
AI Technical Summary
Problems solved by technology
Method used
Image
Examples
Embodiment Construction
[0064] refer to figure 1 , shows an exemplary motor vehicle and is generally indicated by reference numeral 9 . Motor vehicle 9 is illustrated as a passenger car, but it should be understood that motor vehicle 9 may be any type of vehicle, such as a truck, van, sport utility vehicle, or the like. Motor vehicle 9 includes an exemplary propulsion system 10 . It should be understood at the outset that while a rear-wheel drive propulsion system 10 has been illustrated, the motor vehicle 9 may have a front-wheel drive propulsion system, an all-wheel drive propulsion system, or four-wheel drive propulsion systems without departing from the spirit and scope of the present disclosure. drive propulsion system.
[0065] Propulsion system 10 generally includes an engine 12 interconnected with a transmission 14 and a final drive unit 16 . Engine 12 may be a conventional internal combustion or electric motor, a hybrid engine, or any other type of prime mover without departing from the s...
PUM
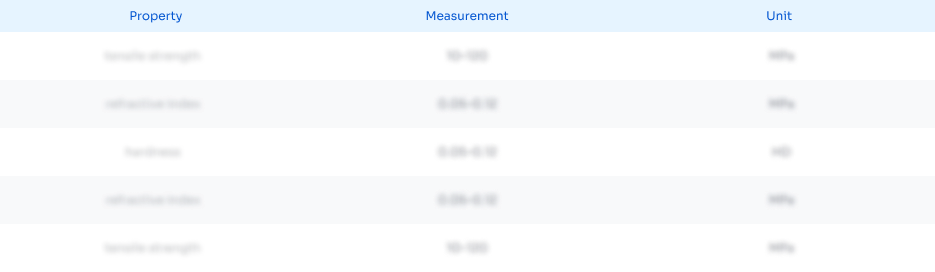
Abstract
Description
Claims
Application Information

- R&D
- Intellectual Property
- Life Sciences
- Materials
- Tech Scout
- Unparalleled Data Quality
- Higher Quality Content
- 60% Fewer Hallucinations
Browse by: Latest US Patents, China's latest patents, Technical Efficacy Thesaurus, Application Domain, Technology Topic, Popular Technical Reports.
© 2025 PatSnap. All rights reserved.Legal|Privacy policy|Modern Slavery Act Transparency Statement|Sitemap|About US| Contact US: help@patsnap.com