A multi-stator multi-rotor motor system based on flexible pcb winding
A multi-rotor, multi-stator technology, applied in the direction of electromechanical devices, electrical components, etc., can solve the problem that the radial flux motor cannot realize the highly integrated motor position detection and drive control, and the miniaturization and light weight of the motor can reach a high level The effect of integration, large moment of inertia, and large output torque
- Summary
- Abstract
- Description
- Claims
- Application Information
AI Technical Summary
Problems solved by technology
Method used
Image
Examples
Embodiment
[0052] Figure 6 A cross-sectional view of a double-stator three-rotor motor system based on flexible PCB windings provided for an embodiment of the present invention. see Figure 6 , the highly integrated dual-stator three-rotor motor system based on flexible PCB windings includes: a stator module, a rotor module, a drive control module and a stator support shaft (2). Among them, the stator module includes: a stator support plate (1), a first flexible PCB winding (7), a second flexible PCB winding (13), and a Hall sensor (24); the rotor module includes: a first rotor back iron (4) , second rotor back iron (18), third rotor back iron (14), first permanent magnet (6), second permanent magnet (9), third permanent magnet (12), fourth permanent magnet (15) , the first copper retaining ring, the second copper retaining ring, the third copper retaining ring, the fourth copper retaining ring, a bearing (22), a bearing end cover (21), and a rotor support plate (23). The first coppe...
PUM
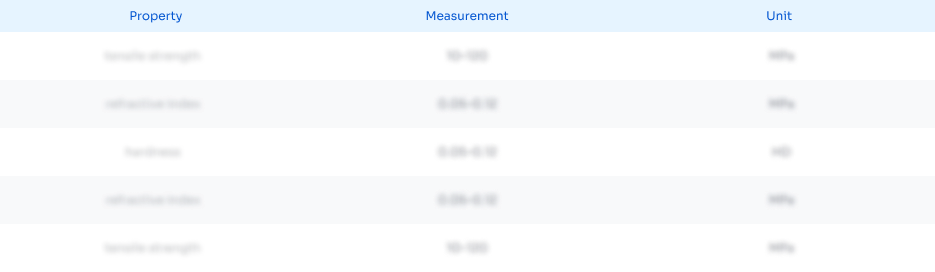
Abstract
Description
Claims
Application Information

- R&D Engineer
- R&D Manager
- IP Professional
- Industry Leading Data Capabilities
- Powerful AI technology
- Patent DNA Extraction
Browse by: Latest US Patents, China's latest patents, Technical Efficacy Thesaurus, Application Domain, Technology Topic, Popular Technical Reports.
© 2024 PatSnap. All rights reserved.Legal|Privacy policy|Modern Slavery Act Transparency Statement|Sitemap|About US| Contact US: help@patsnap.com