A Robot Vision Measuring System Based on External Tracking and Its Calibration Method
A technology of robot vision and calibration method, which is applied in the field of robot vision measurement system based on external tracking and its calibration, can solve the problems of time-consuming and laborious work, low data acquisition efficiency, and small data acquisition amount for marking point layout and cleaning, and avoids problems such as The solution results are different, the solution results are stable, and the measurement accuracy is good
- Summary
- Abstract
- Description
- Claims
- Application Information
AI Technical Summary
Problems solved by technology
Method used
Image
Examples
Embodiment Construction
[0039]In order to make the objectives, technical solutions and advantages of the present invention clearer, the present invention will be further described in detail below with reference to the accompanying drawings and embodiments. It should be understood that the specific embodiments described herein are only used to explain the present invention, but not to limit the present invention. In addition, the technical features involved in the various embodiments of the present invention described below can be combined with each other as long as they do not conflict with each other.
[0040] like figure 2 As shown, a robot vision measurement system based on external tracking is characterized in that, the visual measurement system includes an external tracking device 1, a three-dimensional spherical cage target 2, an area array scanner 3, an industrial robot 4 and a calibration device 5, wherein:
[0041] The area array scanner 3 is disposed at the end of the industrial robot, th...
PUM
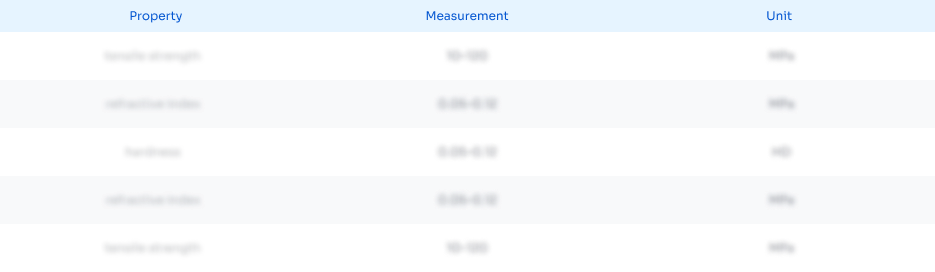
Abstract
Description
Claims
Application Information

- R&D Engineer
- R&D Manager
- IP Professional
- Industry Leading Data Capabilities
- Powerful AI technology
- Patent DNA Extraction
Browse by: Latest US Patents, China's latest patents, Technical Efficacy Thesaurus, Application Domain, Technology Topic, Popular Technical Reports.
© 2024 PatSnap. All rights reserved.Legal|Privacy policy|Modern Slavery Act Transparency Statement|Sitemap|About US| Contact US: help@patsnap.com