A design method of an aero-engine blade simulation part
A technology of aero-engine and design method, applied in computing, special data processing applications, instruments, etc., can solve problems such as no engineering practical value, inability to accurately simulate blade load response, etc., achieving low cost, simple processing, and cost reduction Effect
- Summary
- Abstract
- Description
- Claims
- Application Information
AI Technical Summary
Problems solved by technology
Method used
Image
Examples
Embodiment Construction
[0022] The technical scheme of the design method of an aeroengine blade simulation part of the present invention will be further described below in conjunction with the accompanying drawings.
[0023] Such as figure 1 As shown, the present invention relates to a design method of an aeroengine blade simulation part, and the realization steps are as follows:
[0024] The first step is to determine the basic requirements of the simulation part design and form a test plan. The existing research results show that the effect of laser shock strengthening has a great relationship with the shape and size of the structure, and the strengthening effect of different geometric shapes under the same laser strengthening parameters is very different. In order to ensure that the strengthening effect of the test piece is similar to that of the real blade, truly reflect the distribution of the residual stress of the blade after laser shock strengthening, and improve the possibility of applying ...
PUM
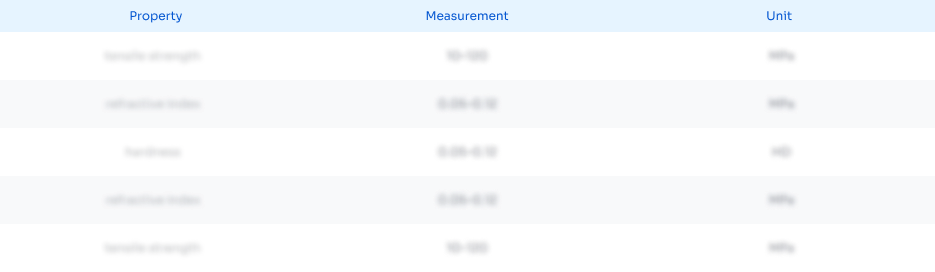
Abstract
Description
Claims
Application Information

- Generate Ideas
- Intellectual Property
- Life Sciences
- Materials
- Tech Scout
- Unparalleled Data Quality
- Higher Quality Content
- 60% Fewer Hallucinations
Browse by: Latest US Patents, China's latest patents, Technical Efficacy Thesaurus, Application Domain, Technology Topic, Popular Technical Reports.
© 2025 PatSnap. All rights reserved.Legal|Privacy policy|Modern Slavery Act Transparency Statement|Sitemap|About US| Contact US: help@patsnap.com