A composite material wing positioning structure assembly and demoulding integrated tooling and using method thereof
A positioning structure and composite material technology, applied in the field of composite material molding, can solve the problems of scratching the joint shaft hole matching shaft hole, the mold shaft hole affecting the positioning shaft assembly and disassembly process, and it is difficult to ensure the vertical angle of the positioning shaft. The operability and promotion and application value, the effect of solving the damage and reducing the risk
- Summary
- Abstract
- Description
- Claims
- Application Information
AI Technical Summary
Problems solved by technology
Method used
Image
Examples
Embodiment Construction
[0044] In order to make the purpose, technical solutions and advantages of the embodiments of the present invention clearer, the technical solutions in the embodiments of the present invention will be clearly and completely described below in conjunction with the drawings in the embodiments of the present invention. Obviously, the described embodiments It is a part of embodiments of the present invention, but not all embodiments. Based on the embodiments of the present invention, all other embodiments obtained by persons of ordinary skill in the art without making creative efforts belong to the protection scope of the present invention.
[0045] A composite material wing positioning structure assembly and demoulding integrated tooling and its use method, combined with figure 1 , figure 2 , including support 1, flange 2, pressure block 3 and lead screw 4, support 1 is a door-shaped steel frame, lead screw 4 is threaded in the middle of the top of support 1, and the length dir...
PUM
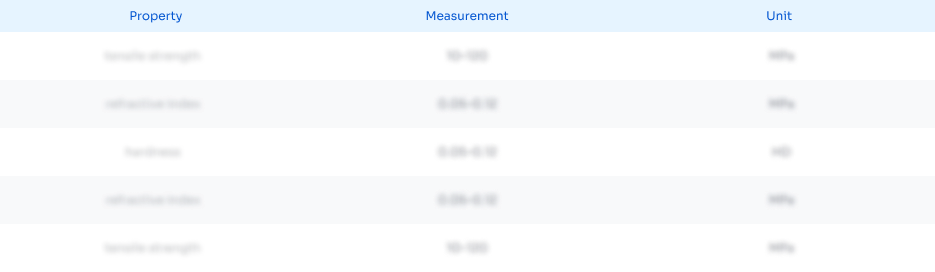
Abstract
Description
Claims
Application Information

- R&D
- Intellectual Property
- Life Sciences
- Materials
- Tech Scout
- Unparalleled Data Quality
- Higher Quality Content
- 60% Fewer Hallucinations
Browse by: Latest US Patents, China's latest patents, Technical Efficacy Thesaurus, Application Domain, Technology Topic, Popular Technical Reports.
© 2025 PatSnap. All rights reserved.Legal|Privacy policy|Modern Slavery Act Transparency Statement|Sitemap|About US| Contact US: help@patsnap.com