Inverse solution method, device and robot of mechanical arm
A technology of manipulator and arm length, which is applied in the field of manipulators, can solve problems such as the complexity of the inverse solution process of six-axis manipulators, and achieve the effect of increasing speed and ensuring timeliness
- Summary
- Abstract
- Description
- Claims
- Application Information
AI Technical Summary
Problems solved by technology
Method used
Image
Examples
Embodiment 1
[0029] According to an embodiment of the present invention, an embodiment of an inverse solution method of a robotic arm is provided. It should be noted that the steps shown in the flow chart of the accompanying drawings can be executed in a computer system such as a set of computer-executable instructions, Also, although a logical order is shown in the flowcharts, in some cases the steps shown or described may be performed in an order different from that shown or described herein.
[0030] figure 1 is a flow chart of an inverse solution method for a mechanical arm according to an embodiment of the present invention, such as figure 1 As shown, the method includes the following steps:
[0031] Step S102, according to the task to be performed of the robot arm, select the first rotation axis among the multiple rotation axes of the robot arm, wherein the first rotation axis and the target point have a positional relationship corresponding to the task to be performed, and the targ...
Embodiment 2
[0075] According to an embodiment of the present invention, an embodiment of an inversion device for a mechanical arm is provided, Figure 4 is a schematic diagram of an inversion device for a mechanical arm according to an embodiment of the present invention, such as Figure 4 As shown, the device includes:
[0076] The selection module 40 is used to select the first rotation axis among the plurality of rotation axes of the robot arm according to the task to be performed by the robot arm, wherein the first rotation axis and the target point have a positional relationship corresponding to the task to be performed, and the target point is used to represent the The position that the actuator connected to the end robot arm needs to reach when performing the task to be performed.
[0077] The first determining module 42 is configured to determine the position parameter of the first rotating shaft according to the target point and the positional relationship between the first rota...
Embodiment 3
[0100]According to an embodiment of the present invention, a robot is provided, including the inverse solution device of the mechanical arm described in Embodiment 2.
PUM
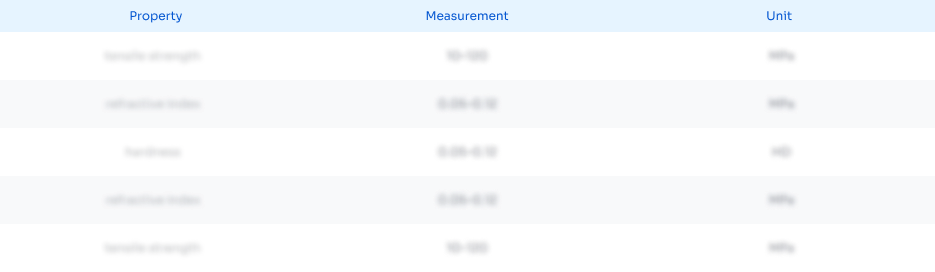
Abstract
Description
Claims
Application Information

- Generate Ideas
- Intellectual Property
- Life Sciences
- Materials
- Tech Scout
- Unparalleled Data Quality
- Higher Quality Content
- 60% Fewer Hallucinations
Browse by: Latest US Patents, China's latest patents, Technical Efficacy Thesaurus, Application Domain, Technology Topic, Popular Technical Reports.
© 2025 PatSnap. All rights reserved.Legal|Privacy policy|Modern Slavery Act Transparency Statement|Sitemap|About US| Contact US: help@patsnap.com